Shape to Fabrication '25: Major Themes
Major takeaways from Shape to Fabrication '25, and the interesting practitioners driving change in our industry
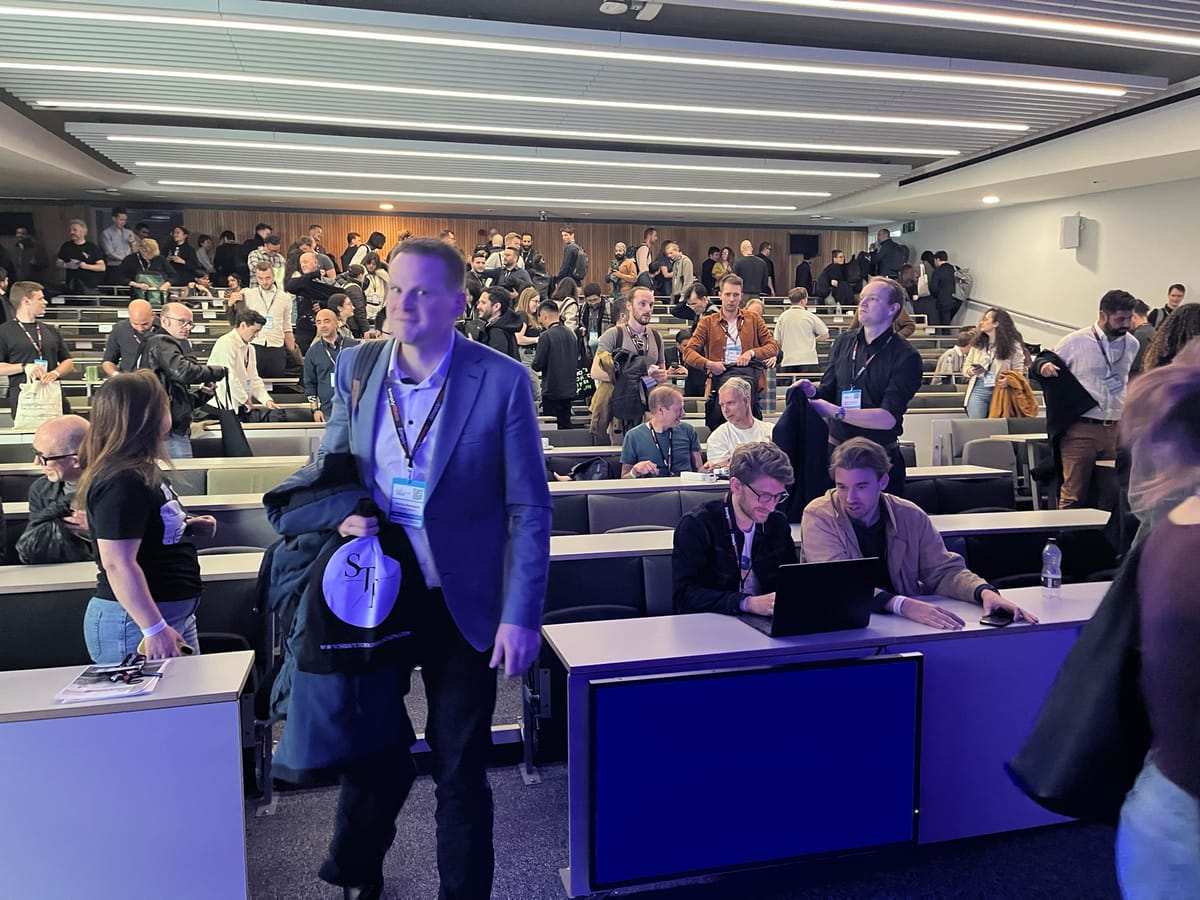
At this year's Shape to Fabrication conference, hosted by UK reseller/training consultant SimplyRhino at the University of Westminster in London, there were 23 different presentations across the two day conference. Preceding the main event was a workshop day as well as the Rhino New Developments Day, which was hosted by McNeel and featured mostly updates from the McNeel dev team. I'll cover those events in another post and for now just focus on the main conference days. In reviewing my notes from this marathon of ideas and explanation, a few key themes started to emerge.
Theme 1: Computational design is no longer optional but rather required for ambitious architecture, both in design and execution.
Ok, perhaps that's a bit of a provocative statement. There are no doubt many who would disagree, yet I did see several projects from ambitious design practices whose form and construction would not have been possible without a concentrated effort to integrate computational practices with every stage of the project. Here are a few featured design projects that leveraged computation to achieve their success:
Crafting Contemporary Cities: Xi’an CCBD
Luis Sacrastán Murga, Heatherwick Studio
Pablo Zamorano, Heatherwick Studio
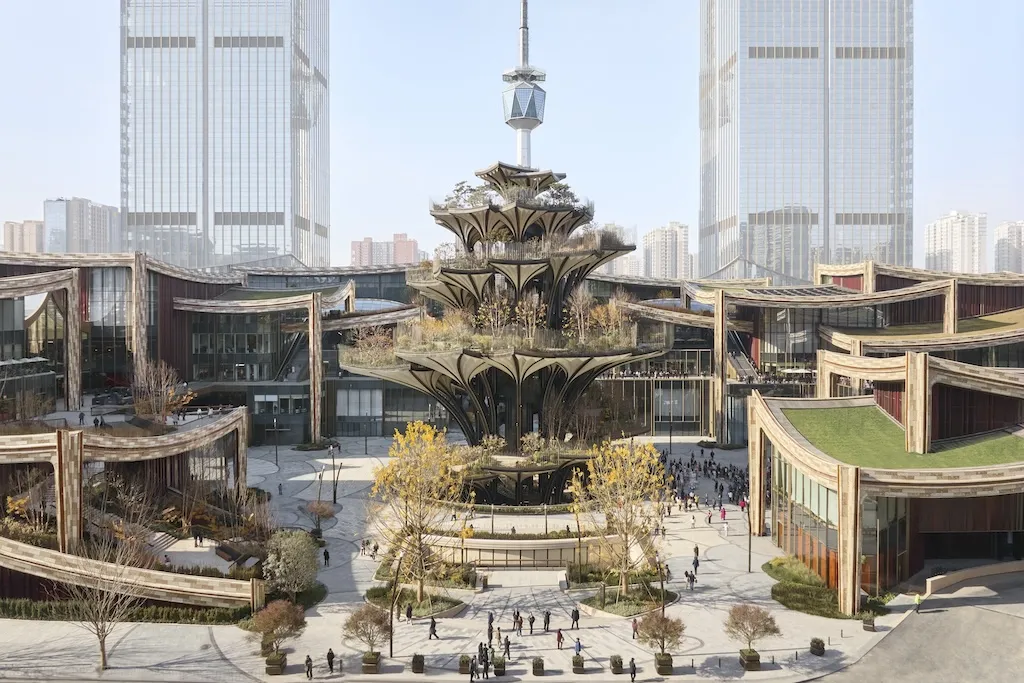
Heatherwick Studios maintains a team of 5 computational design specialists and about 10-12 computational designers working directly on projects. This 91,000 sqm project in Xi'an employed computational methods in master planning, massing, structural system assignment, as well as formal exploration, as seen in the large, sculptural tree structure that serves as the social focal point for the entire project.
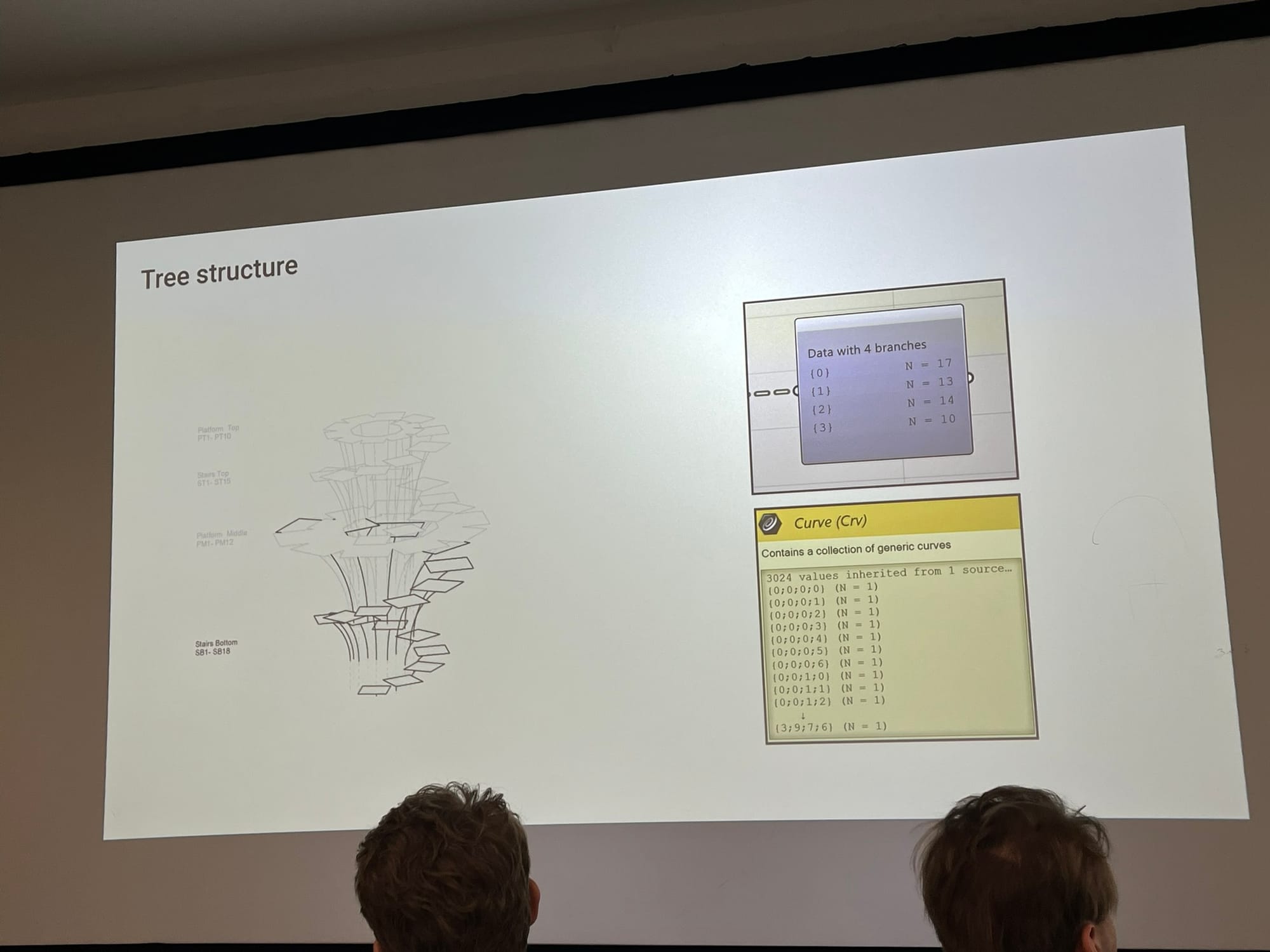
Crafting a Jewel: A Collaborative Journey Through Design and Delivery of the Old War Office Pavilion
Michal Wojtkiewicz, Daewha Kang Design
Maria Meizoso Aguilar, Octatube
Daniel Van Kersbergen, Octatube
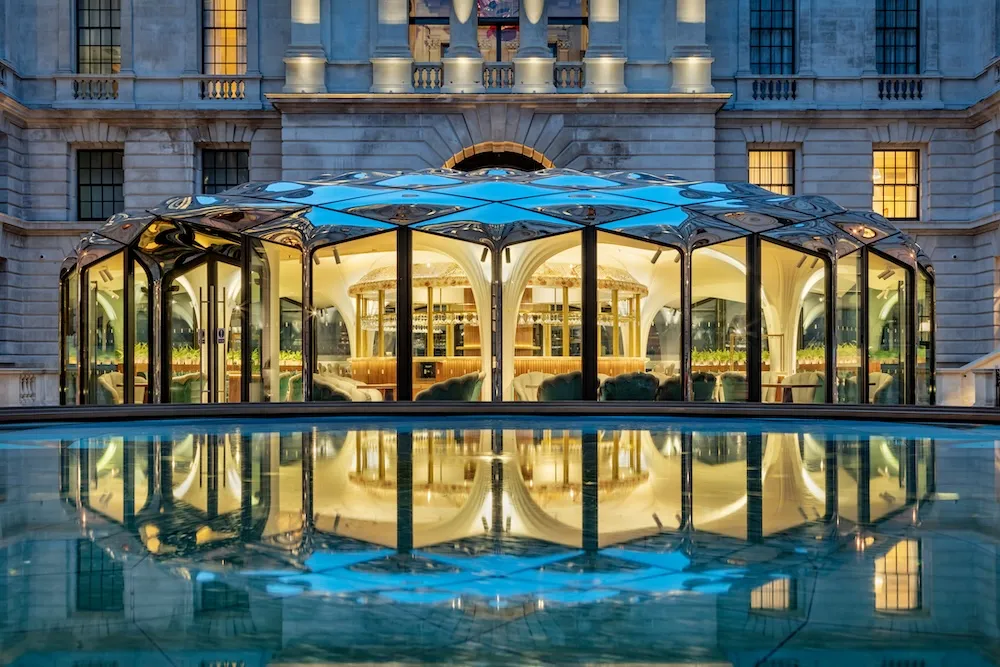
Nestled into the central courtyard of the Old War Office, an historic Edwardian structure located in Whitehall, London, this pavilion/restaurant was designed and fabricated to a high level of exactness. The design is, of course, parametric, with the geometry of everything computationally scrutinized. The mirror finish of the roof panels prompted the design team to commission a reflectivity study from Arup, revealing potential problems at certain times of the day in certain seasons, leading to a rethinking of the curvature for each panel.
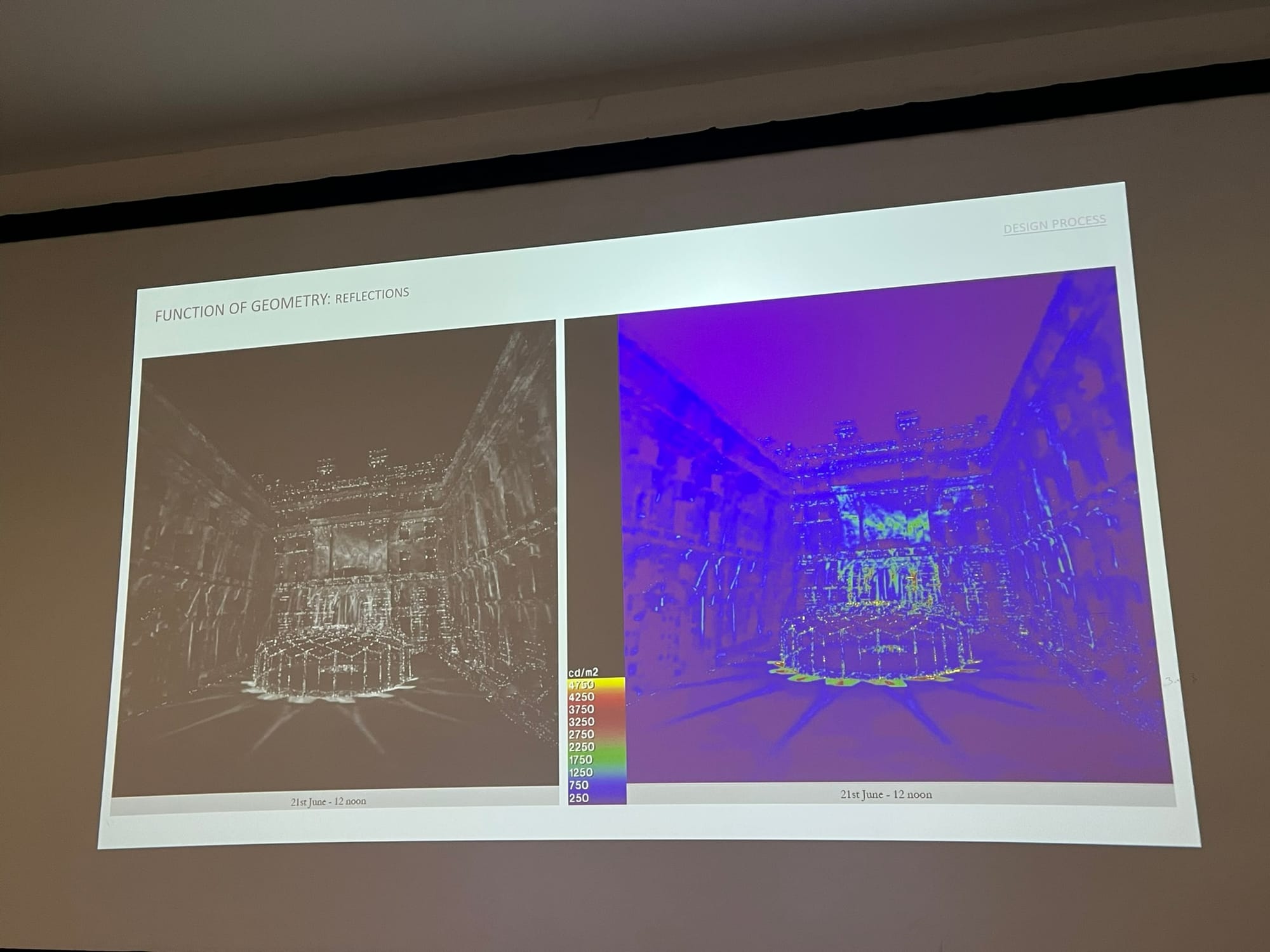
Shaping Complexity: Digital Strategies for large-scale Infrastructure Design
Andy Barnes, Grimshaw
Ester Rubio Madroñal, Grimshaw
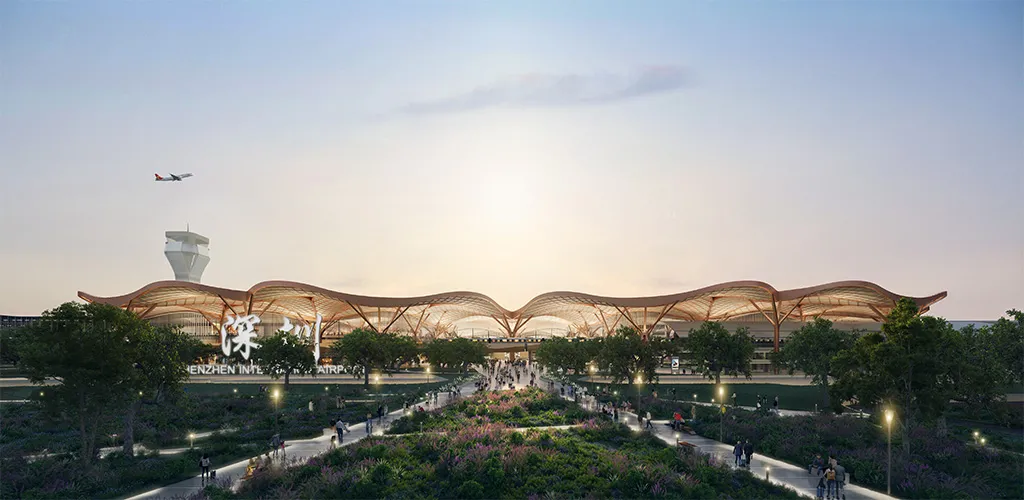
For the Shenzhen Airport, Grimshaw's design technology team developed a hierarchical chain of Grasshopper scripts to manage the design, development, and documentation of this huge project. Conceptual geometry was defined computationally in a primary script that could be referenced by others as needed, to ensure that the design's concept had a common source of truth. This project also made heavy use of Rhino.Inside.Revit to automate documentation for the roof structure as well as to automatically generate detailed mesh geometry for a separate visualization-only Revit model.
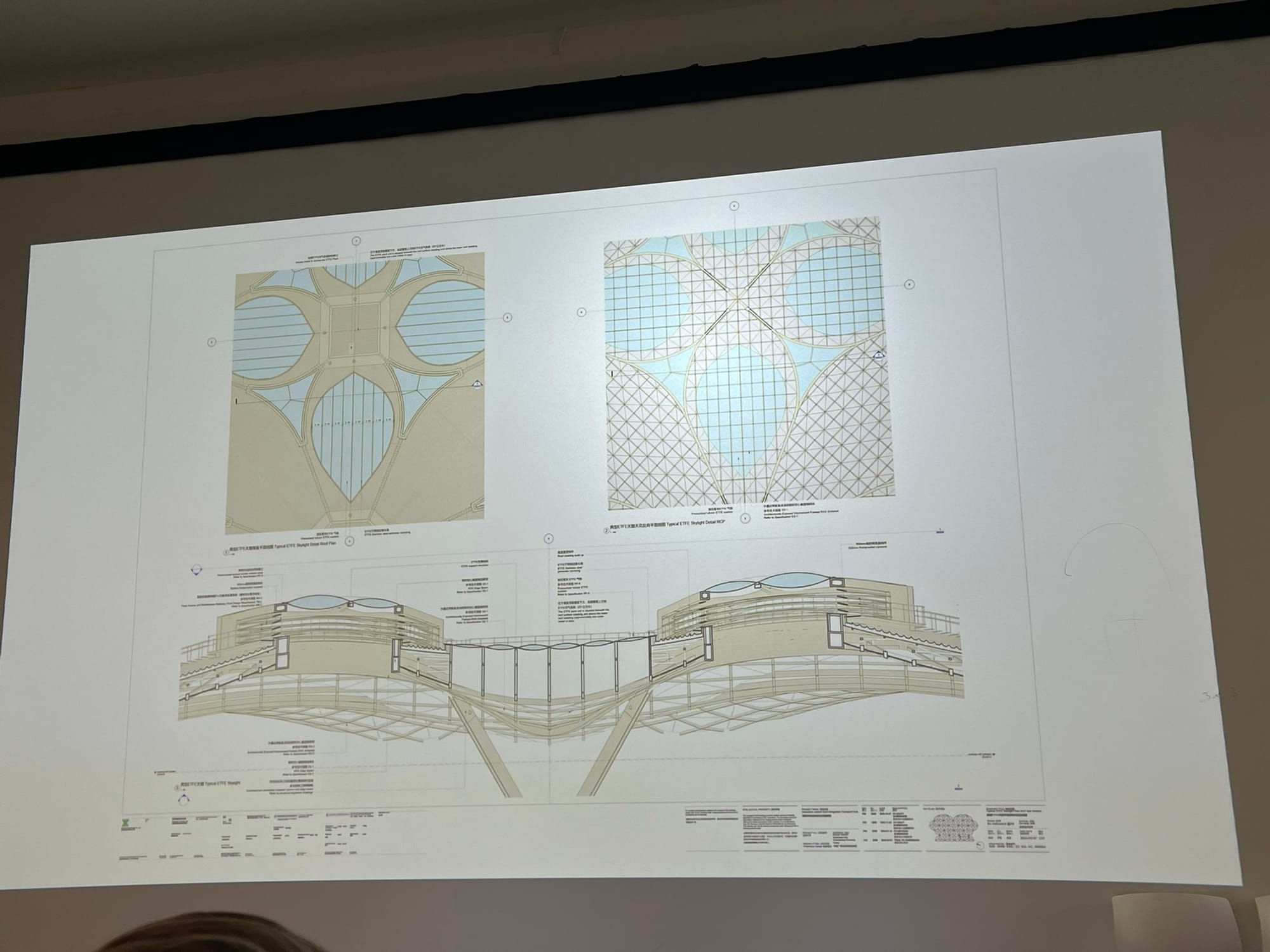
Theme 2: Rigorous data management and automation for fabrication and assembly is becoming increasingly common.
This was perhaps the most prevalent theme across all presentations for the entire conference. I noted eight different firms whose presentations fit this category (perhaps a few too many to be featured fully here). Here are some highlights from digital fabrication and construction assembly.
3DStairDesigner: Automated Workflow for Complex Concrete 3D-Printed Stairs
Philip Schneider, Scawo3D
Timo Harboe, Timo Harboe APS
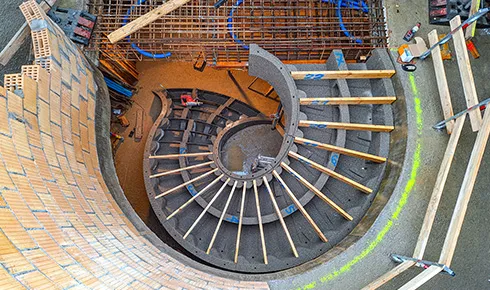
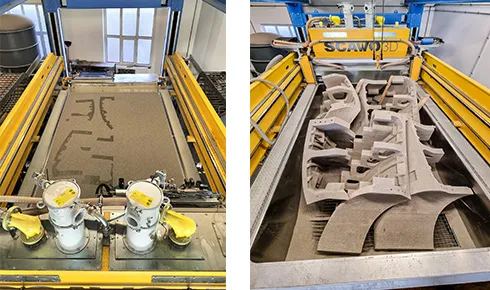
It's common to see the development of new manufacturing processes go hand-in-hand with new computational developments (there's a reason why "robotics" is not only an area of manufacture but also a specialty in computer science departments across the world). The South Tyrolian large-scale 3D printing company Skawo3D has invented a new form of printing called "selective paste intrusion" (think 3d inkjet printer for cementitious aggregate) that can easily churn out large volumes of quite highly-detailed detailed concrete parts. To enter into the market of architectural elements, Skawo3D's resident computational specialist, Philip Schneider, teamed up with computational design consultancy Timo Harboe APS to develop a fully automated stair generation tool that can accept site constraints and design inputs and generate high-resolution closed mesh geometry that is able to be sent straight to the printer. With their design automation, modeling time for these complex stair geometries was reduced by 95%.
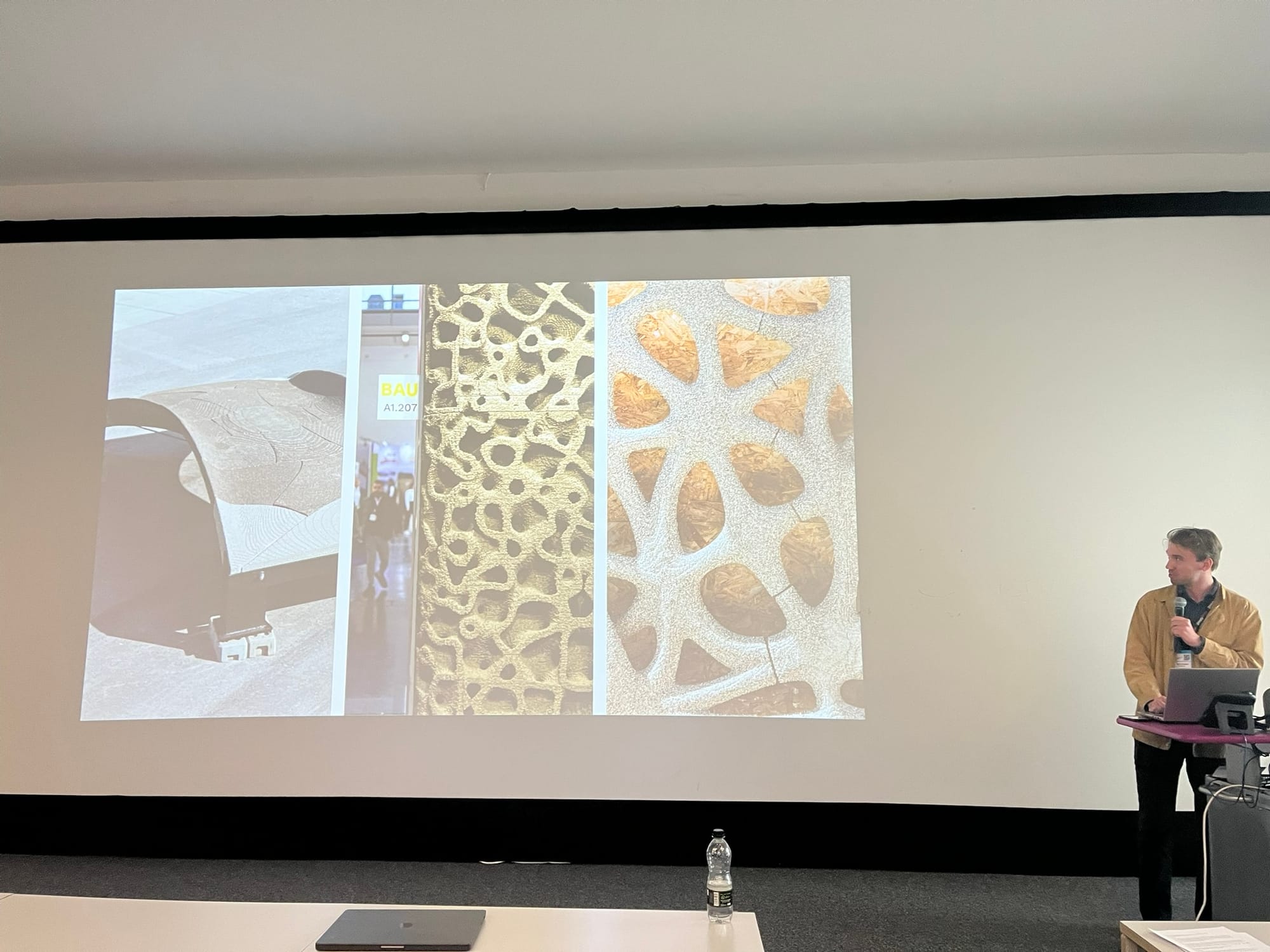
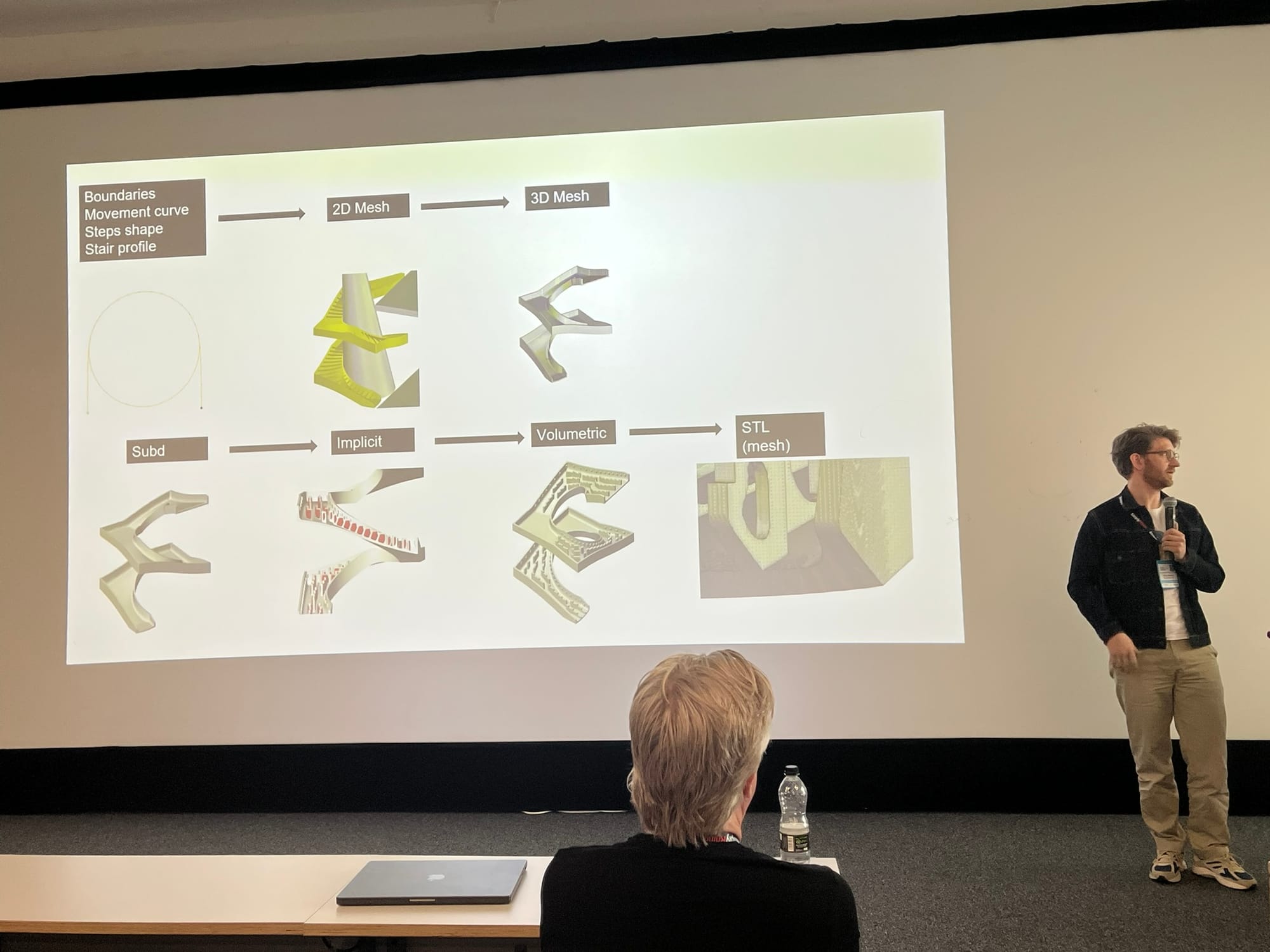
Handling Complexity on a Manufacturing Level
Martin Manegold, Digitales Bauen
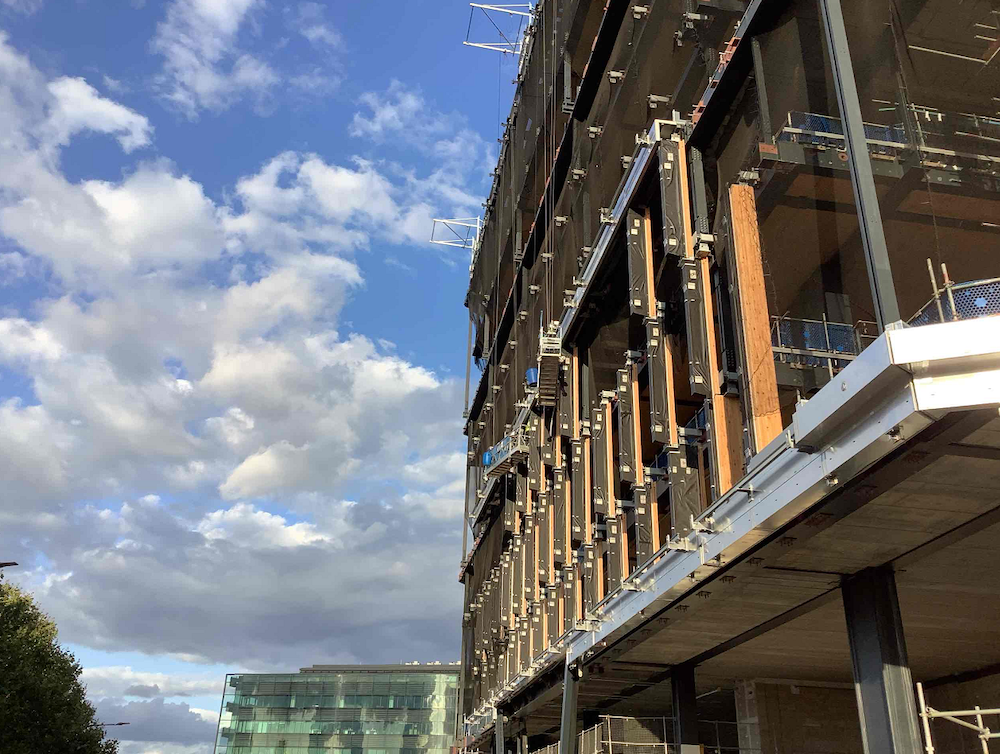
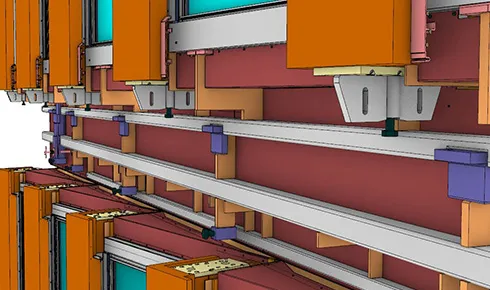
Martin Manegold delivered an impressive presentation on managing exceedingly complex facade assemblies using just Rhino and Grasshopper. For the KGX1 Google "groundscraper" (330m-long 1M sq ft building in King's Cross, London), Digitales Bauen managed 7,000 different assemblies, comprised of 31,000 unique parts with a team of 12 computational designers and engineers. In total, the amount of geometric data exceeded 4tb (excluding backup files). Similar to Grimshaw's workflow detailed above, Digitales Bauen employed "reference models" that encompassed multiple scopes of detail, "abstract models" that were used exclusively as input for Grasshopper scripts, and a custom project-specific Grasshopper plugin that facilitated the creation of data-rich facade assembly blocks. The main message of the presentation was on managing complexity—addressing it early and putting a focus on it throughout the entire process.
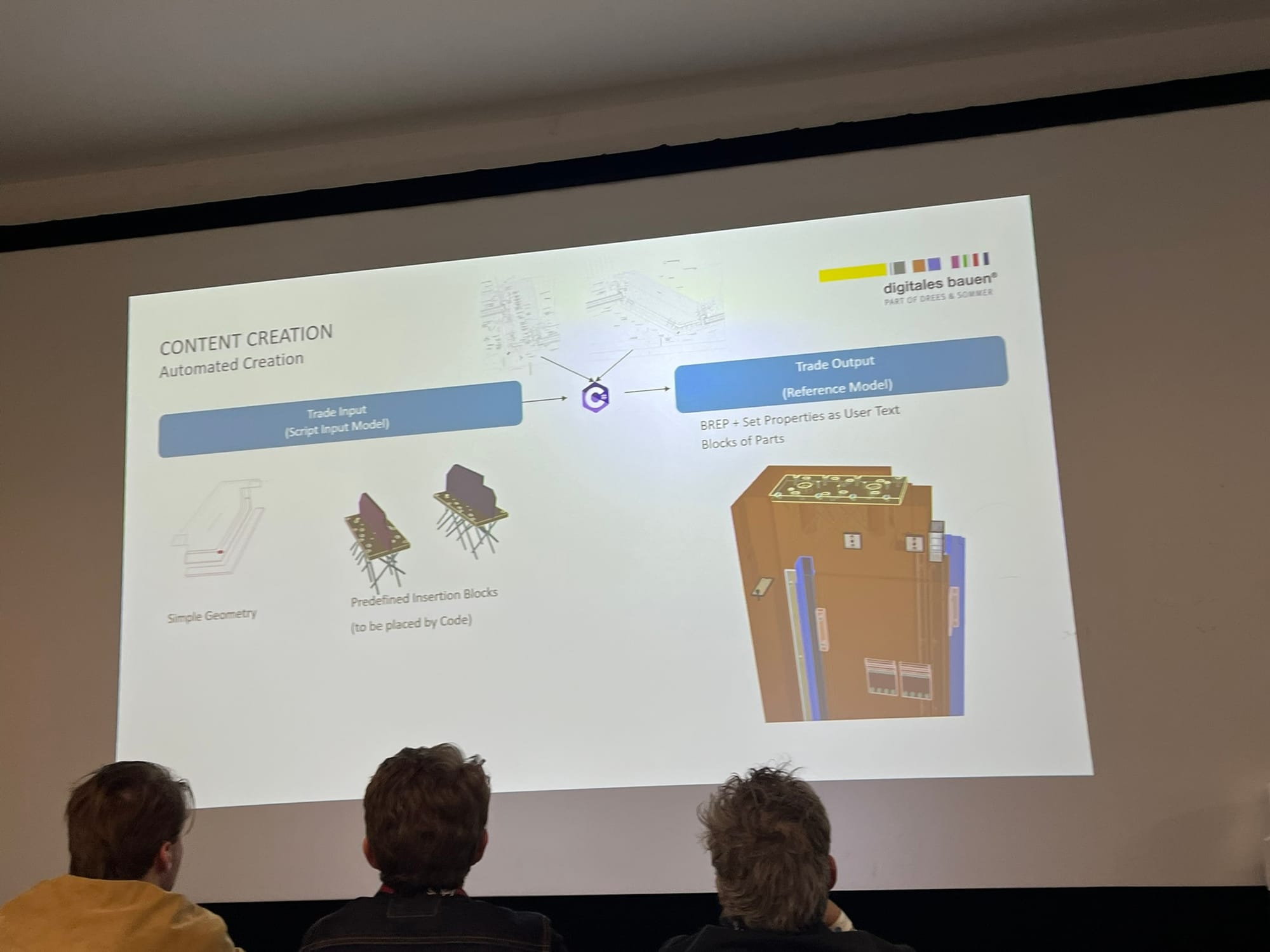
Data-storage experiments for managing complexity in timber projects
Harri Lewis, Mule Studio
Gianluca Tabellini, Mule Studio
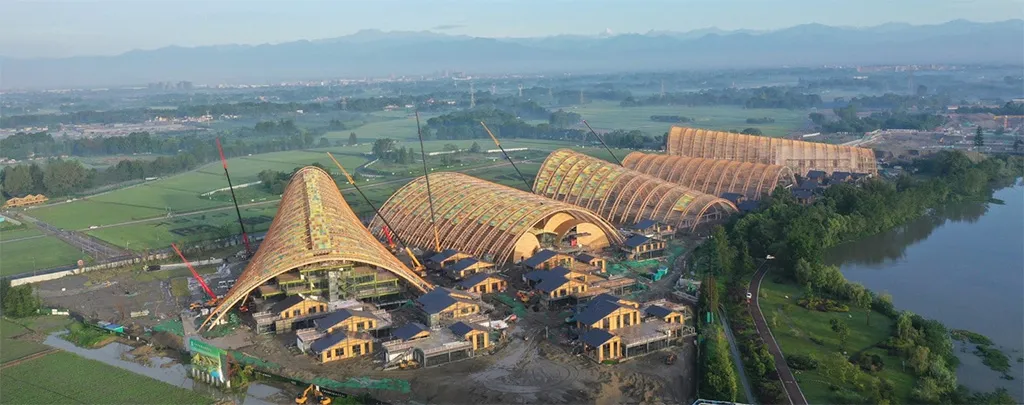
In this presentation, Harri Lewis and Gianluca Tabellini of British design agency Mule Studio detailed how they manage complex project through a few different methods, each suited to projects of different scales. For small-scale projects, using Rhino as its own database is sufficient, and comes with the benefit of having a Rhino model or Grasshopper script be the single source of truth for project geometry. With added scale and complexity, Mule employs custom C# class libraries to define objects whose geometry is an attribute, along with various other necessary data. These objects can then be serialized into JSON files for storage on a local network. Finally, for projects requiring cloud-based collaboration or storage, the firm relies on Speckle as an endpoint for all their custom object scripting.
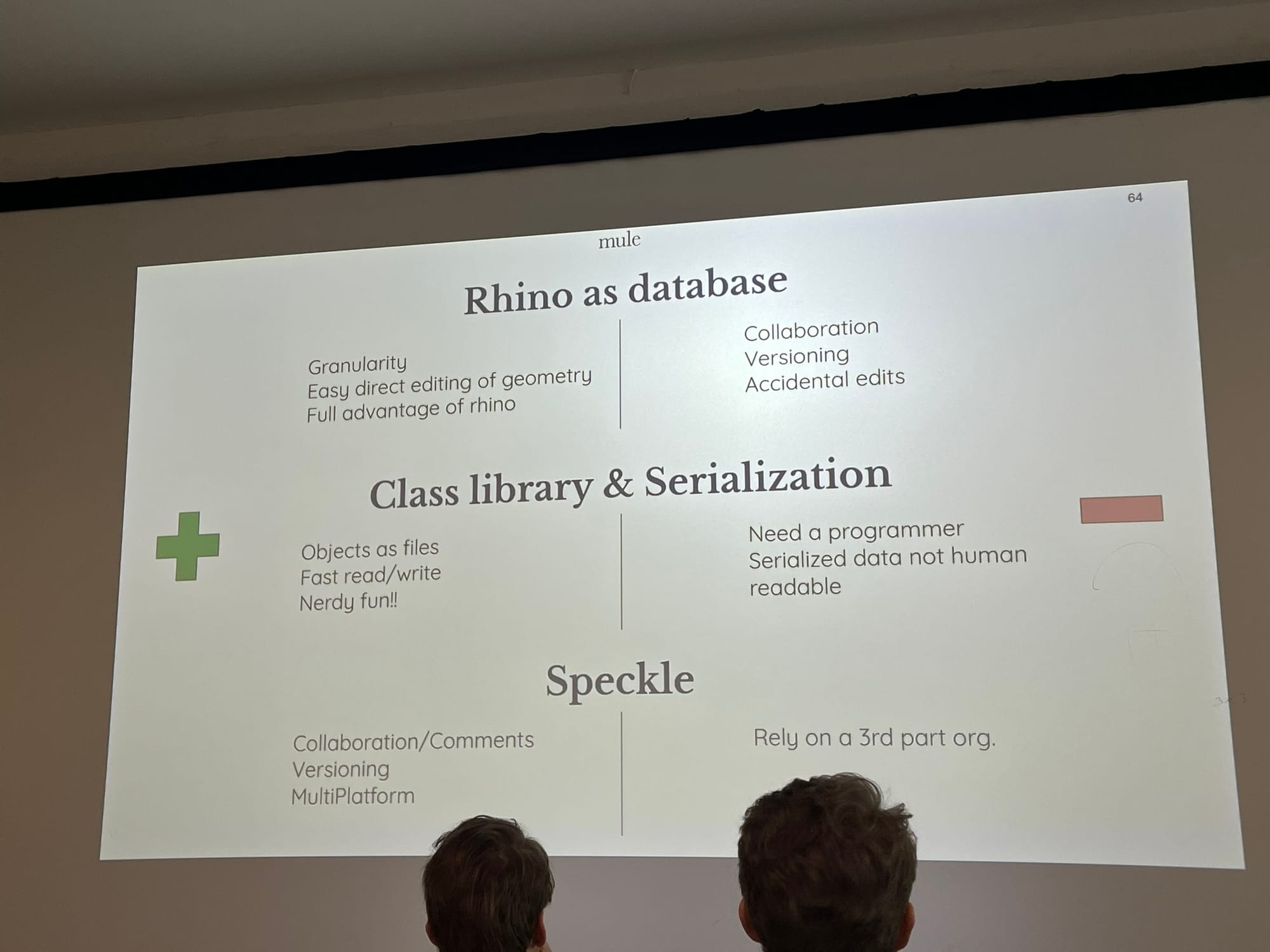
Theme 3: New tools for Rhino and Grasshopper are increasingly sophisticated and ambitious.
One thing I've been hearing a lot from various people in the industry is that Rhino/Grasshopper is slowly evolving from a standalone design tool that happens to be easily extensible into a fully-fledged experimentation and development platform for quite sophisticated AEC software products. Over the past few years I've observed a few key players, such as ShapeDiver and Speckle, emerge as dynamic companies offering really powerful advancements to the Rhino/Grasshopper community, but it was nice to see some other entrants to the field. There are now entire companies and R&D departments founded on the premise that it is not only possible, but also feasible and worthwhile to add value to some small niche area of 3d modeling in Rhino.
MKS DTECH: Design. Data. Collaboration.
Mikael Santrolli, MKS DTECH
Maruo Sabiu, MKS DTECH
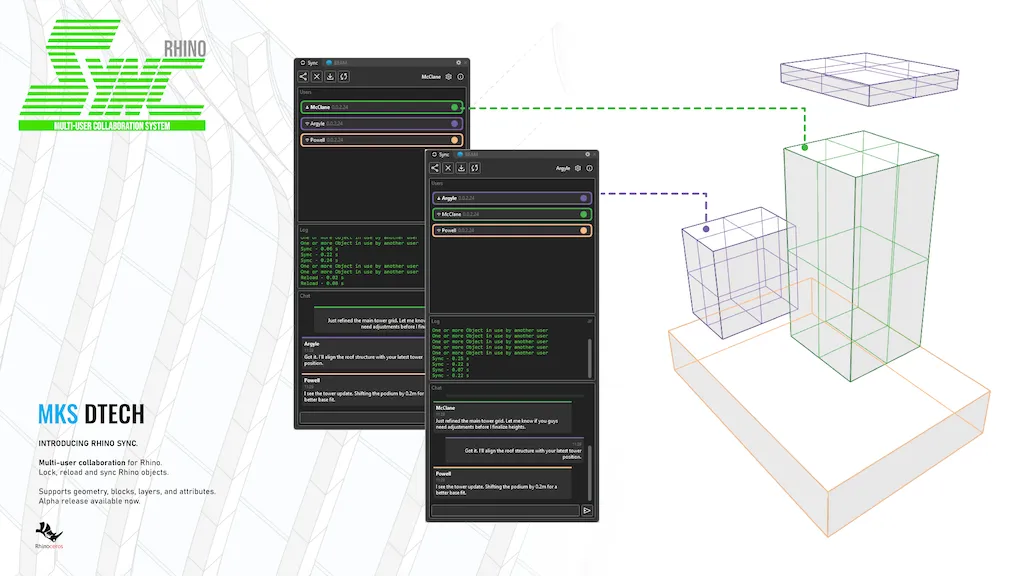
Many are familiar with MKS DTECH's Beam software for generating Revit families from Rhino objects. At Shape to Fabrication, company founders Mikael Santrolli and Maruo Sabiu revealed their next product, Rhino Sync, which essentially aims to allow people to interact with 3dm files in the same manner as they would with a workshared Revit model. Users "check out" individual objects by interacting with them; Rhino Sync will prevent other users from manipulating those objects until the original user has synced back to the central file. The plugin also features a chat interface, and can highlight which objects are checked out by which user. I happen to have actually already tried out this plugin (it's completely free for the moment, though it's still in alpha), and I think that the promise is quite huge (provided it works smoothly and seamlessly—though we don't ask the same of Revit, so maybe I'm being too harsh). Every design team at my firm wastes terabytes of storage by needlessly copying design models back and forth so each can work on his or her own little part; being able to have a central model would really simplify collaboration in Rhino.
Next Generation AEC Platform
Jens Kaarsholm, Motif
Michael Drobnik, Herzog & de Meuron
Alfonso Monedero, Heatherwick Studio
Martin Wilding, KPF
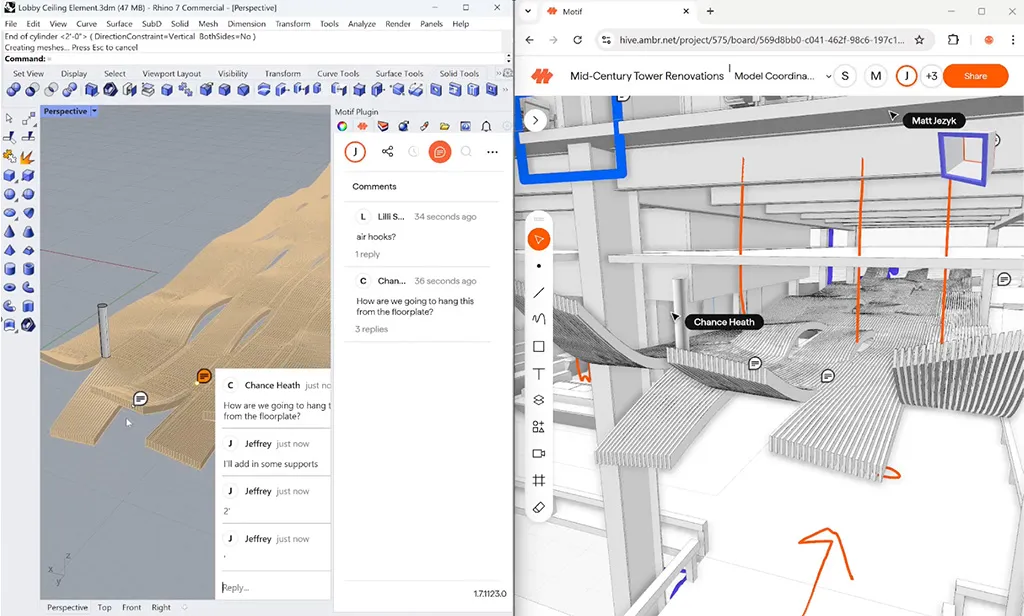
In a nice departure from the usual sponsor product pitches that you see at these conferences, Motif's Director of Product Jens Kaarsholm led a panel discussion with Michael Drobnik, head of design technology at HdM, and Alfonso Monedero and Martin Wilding, both directors of BIM at Heatherwick and KPF, respectively. From what I understand, each played some sort of advisory role in the creation of Motif, which is a new collaboration platform aimed specifically at AEC professionals (think if Miro and Rhino had a baby whose godparent was Bluebeam). The general gist of the discussion was that each of these firms is concerned about the rapid proliferation of design tools from software companies whose aims and motivations are far different from those of architects. By contributing input for the development of Motif, they play a role in shaping software that is actually intended for use by architectural designers (as opposed to more generic industry-agnostic productivity and collaboration tools such as Miro and Bluebeam).
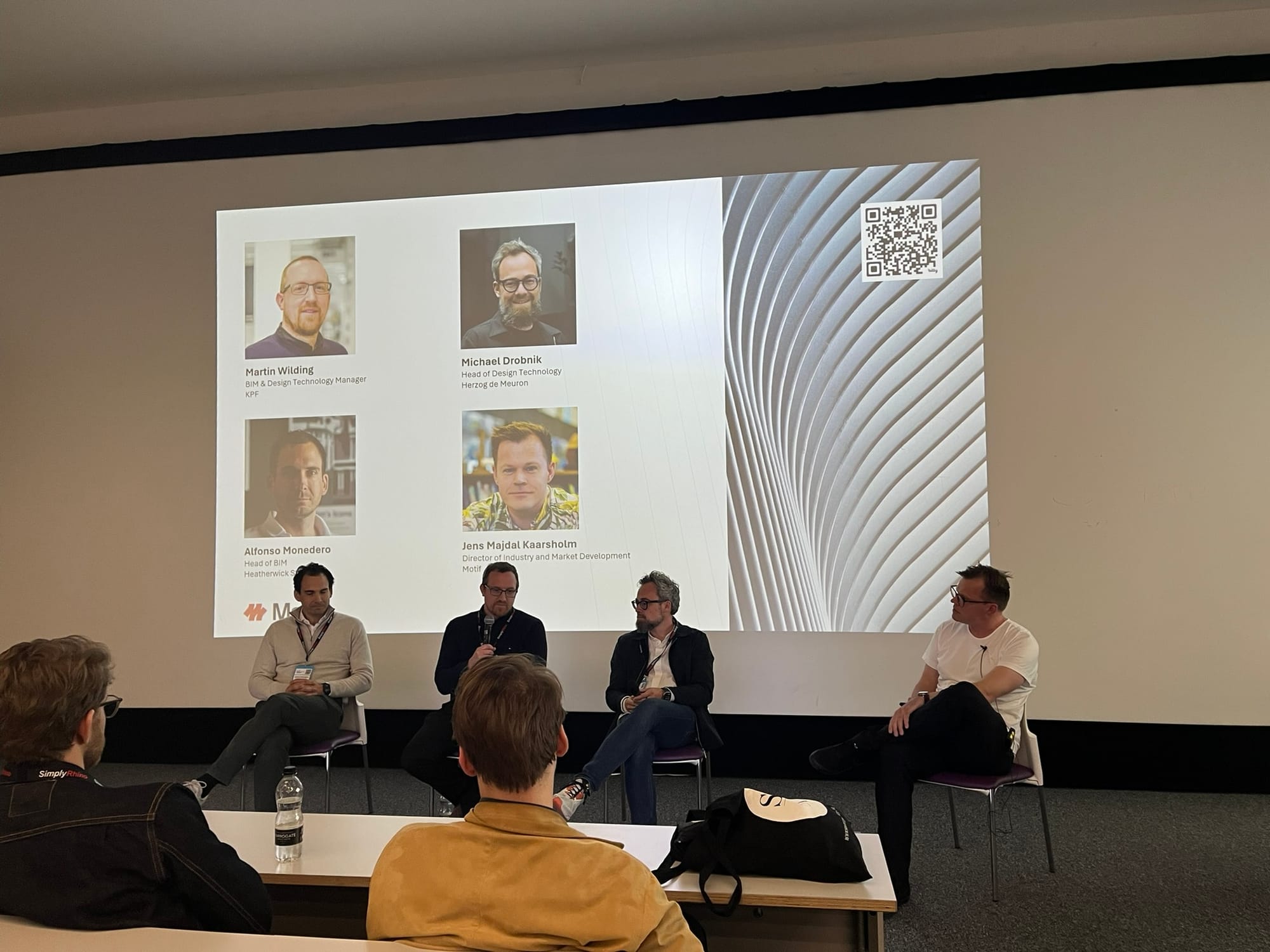
Integrating ecological modeling in Rhino/ Grasshopper
Verena Vogler, McNeel
Eleftherios Kourkopoulos, McNeel
Jens Joschinksi, McNeel
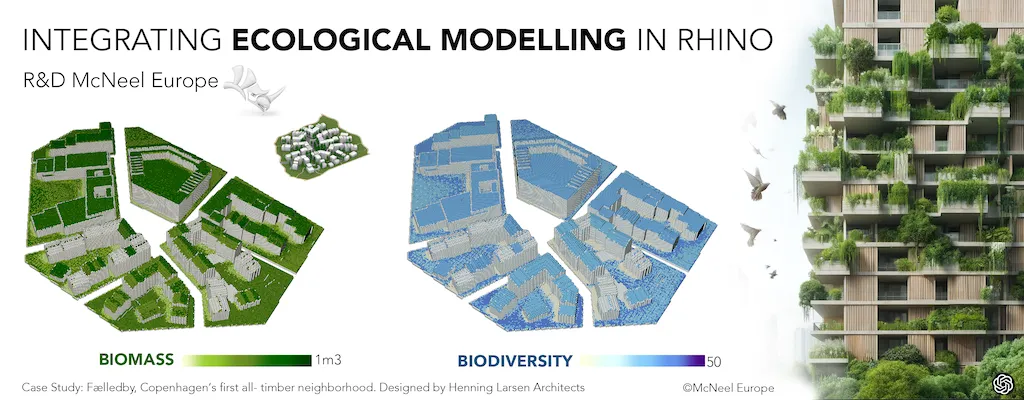
Some Grasshopper plugins are modest, simple utilities that simply extend the functionality of core Grasshopper, add some shortcuts to workflows, or just fill in the gaps (I can modestly say that my own plugin fits squarely within this category, neither particularly innovative nor original). And then there are the truly ambitious ones—plugins that attempt to push the boundary of what Rhino/Grasshopper can reasonably be expected to do (or even what it is for). From the R&D wing of McNeel Europe in Barcelona, we have Rhino.Ecologic, a plugin for ecological simulation within Grasshopper with the aim of performing predictive analysis of the biomass and species diversity surrounding a building over a time-span of decades. Rhino.Ecologic uses a custom ecological simulation model written in C++ and connects it to a novel data-rich voxel-based spatial analysis framework that is extensible to encompass any sort of data the user wishes. While I was in Basel several weeks ago for the Rhino User Meeting there, I was lucky enough to be able to participate in a Rhino.Ecologic workshop hosted by the team. This plugin could be the beginning of something big for Grasshopper. Its two halves are by themselves quite fascinating, yet in concert I would hope to see this employed by designers to make compelling arguments for more actual green life in our buildings and public spaces (not just more greenwashing with the bare minimum of environmental analysis thrown into a concept proposal). The plugin is barely out of alpha (see below for the beta-tester sign up form), and it has quite a bit more development to come, but I will be following this one in the months to come.
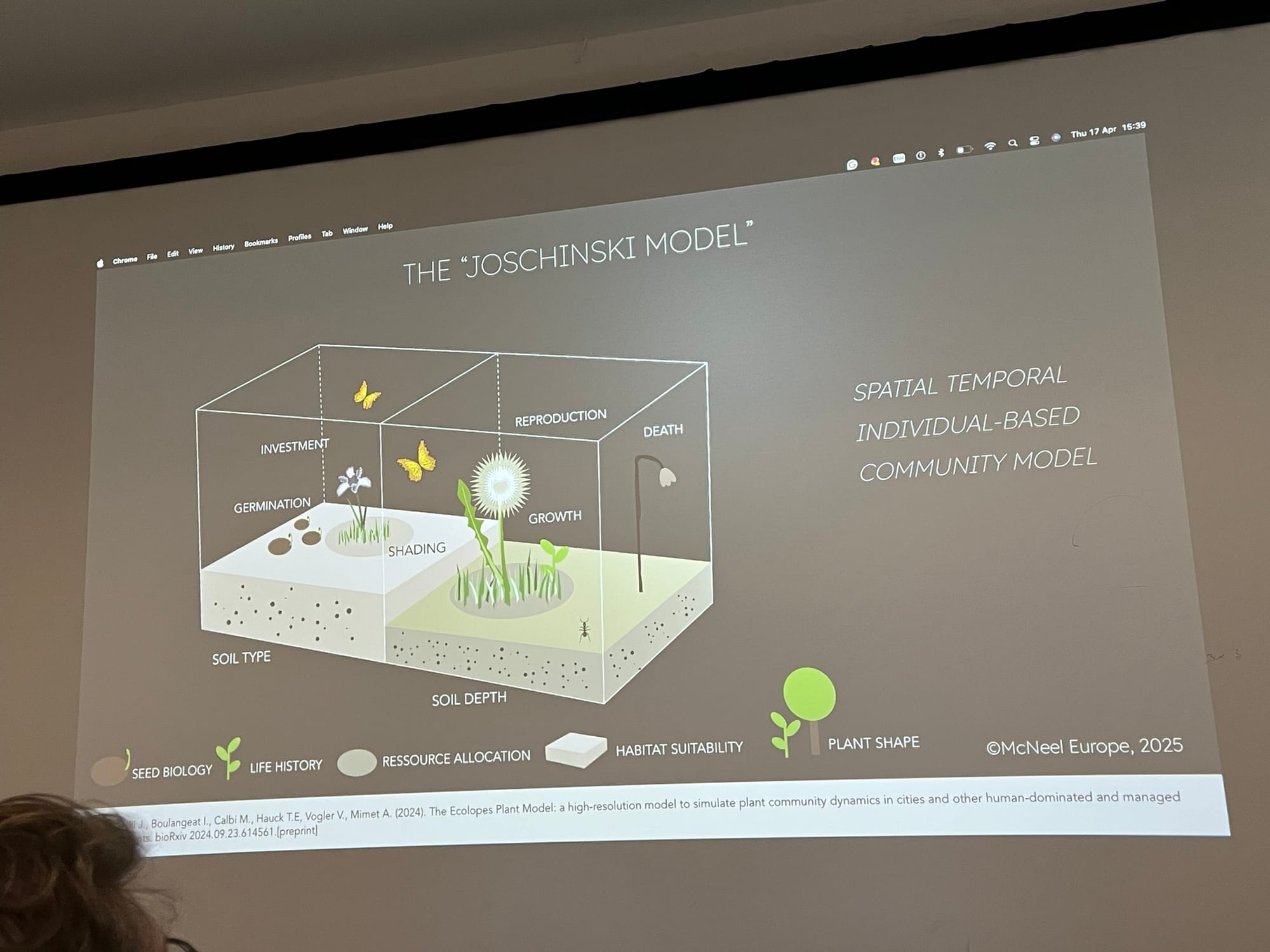
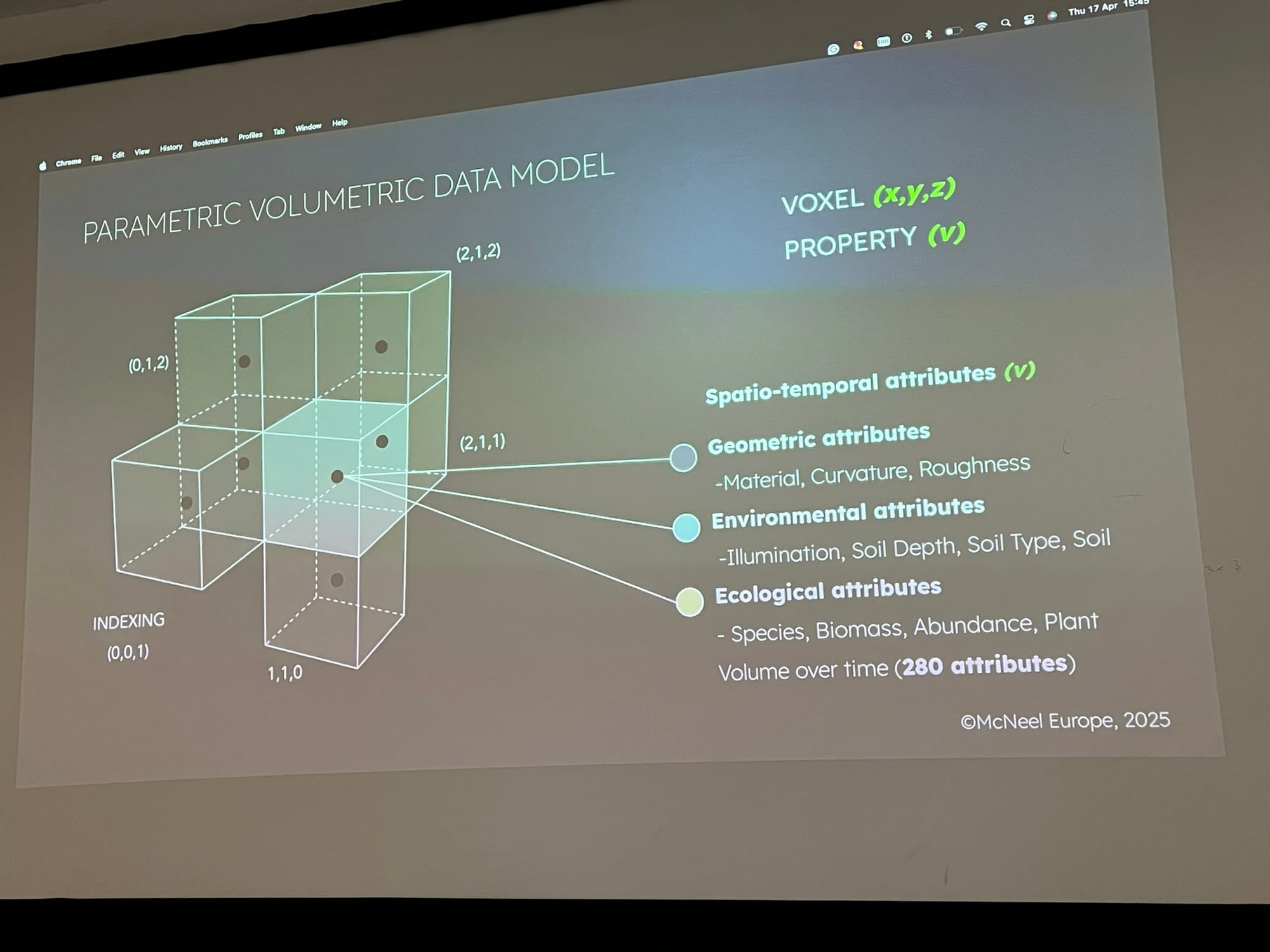
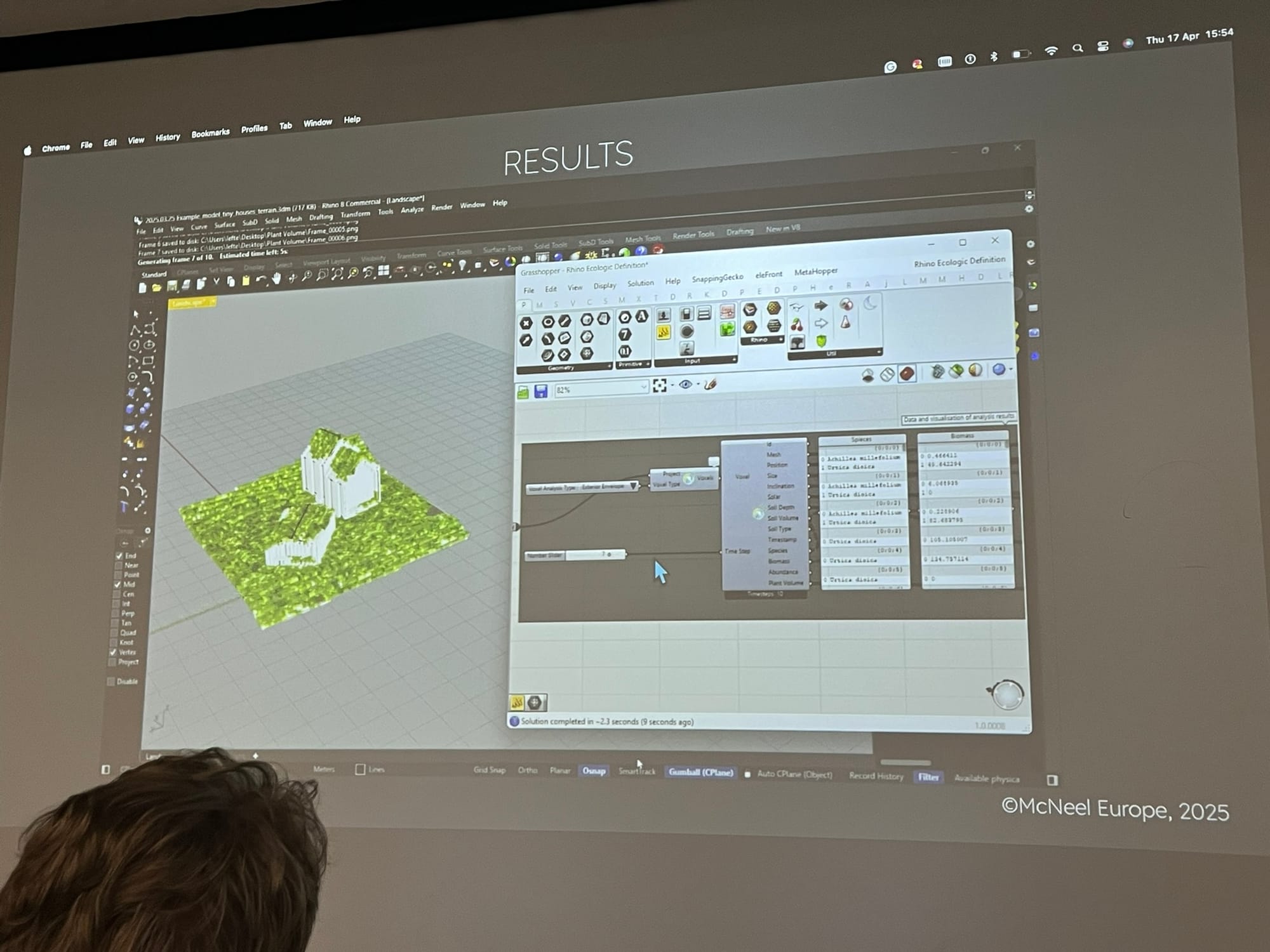
Theme 4: In-house software development continues to drive compelling case studies for AEC, providing a compelling argument for design technology teams to invest resources into learning C# coding and proper software and web development skills.
Continuing on the idea of who's in control over our digital design environments, in the years that I've been working in design technology I've seen an increase in the amount of in-house software development going on at large architecture and engineering firms. Some (like Thornton Tomasetti's CORE Studio) are practically household names among computational designers at this point. Increasingly, firms are investing heavily in software development to maintain a competitive edge or bolster their reputations as leaders in innovation on all fronts, not just in design.
How solving project challenges drives firm-wide innovation
Luc Wilson, KPF
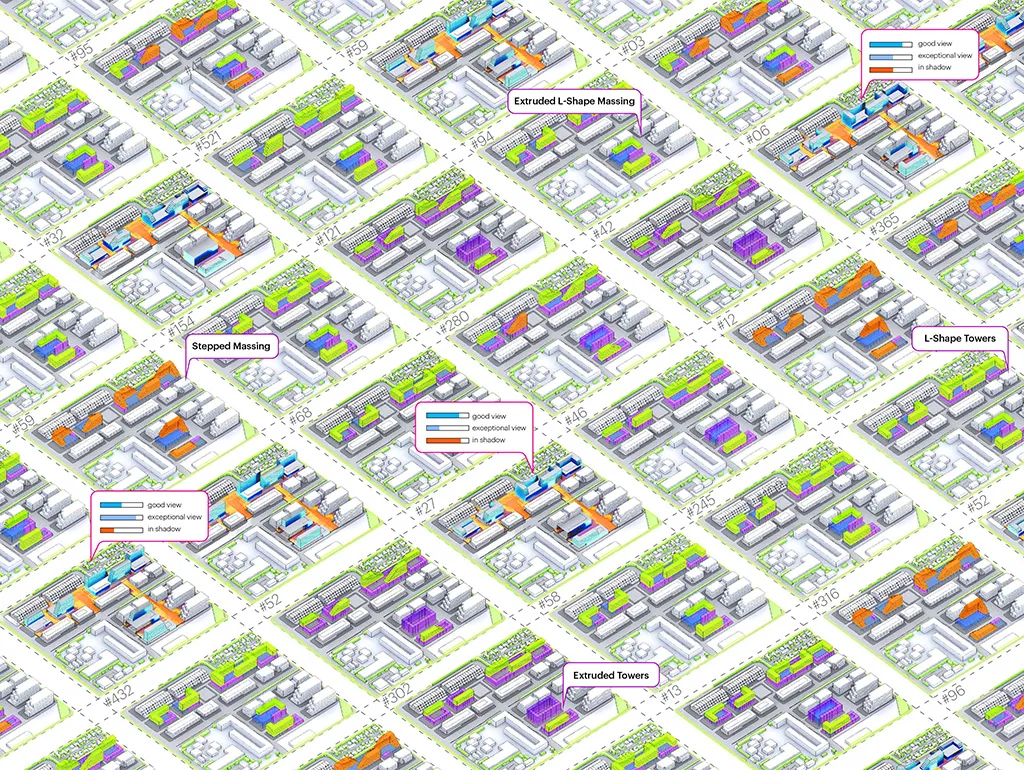
For some time now I've been aware of KPF's embrace of web development as a communications tool for their design technology efforts. The KPFui website features some fun case studies that obviously hint at much more advanced workflows. At Shape to Fabrication, KPFui director Luc Wilson delved into some of the inner workings of KPF's internal tooling and how his team manages deployment of their in-house scripts and utilities for designers to use. The official library of tools for KPF is called DAM (don't ask me what it stands for) and it is completely managed through a git repository that is automatically compiled through Github into a fully-functional internal website every 15 minutes. It's a wonderful idea that any contribution made to the repo is available firm-wide in the time it takes to get a coffee. Of course, everything has to be standardized to fulfill predefined templates, but if you know me you know I'm a big fan of templating in general. KPF also tracks usage of its internal tools through AWS Cloudwatch and has an in-house Grasshopper plugin called Toucan that allows users who are not visual programming experts access their more advanced tools with a procedurally-generated (!) UI that runs Grasshopper scripts asynchronously using Rhino.Compute. Impressive.
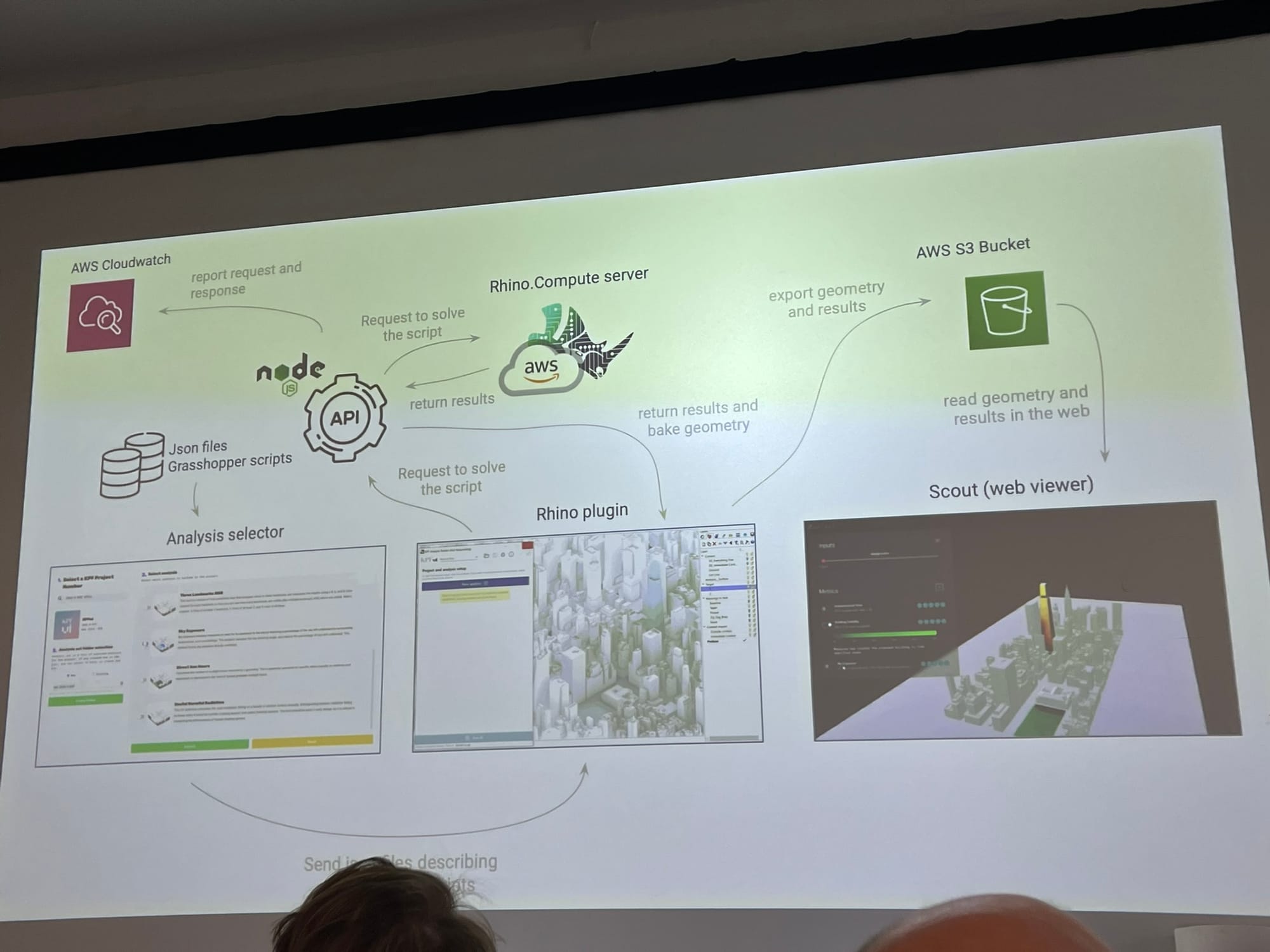
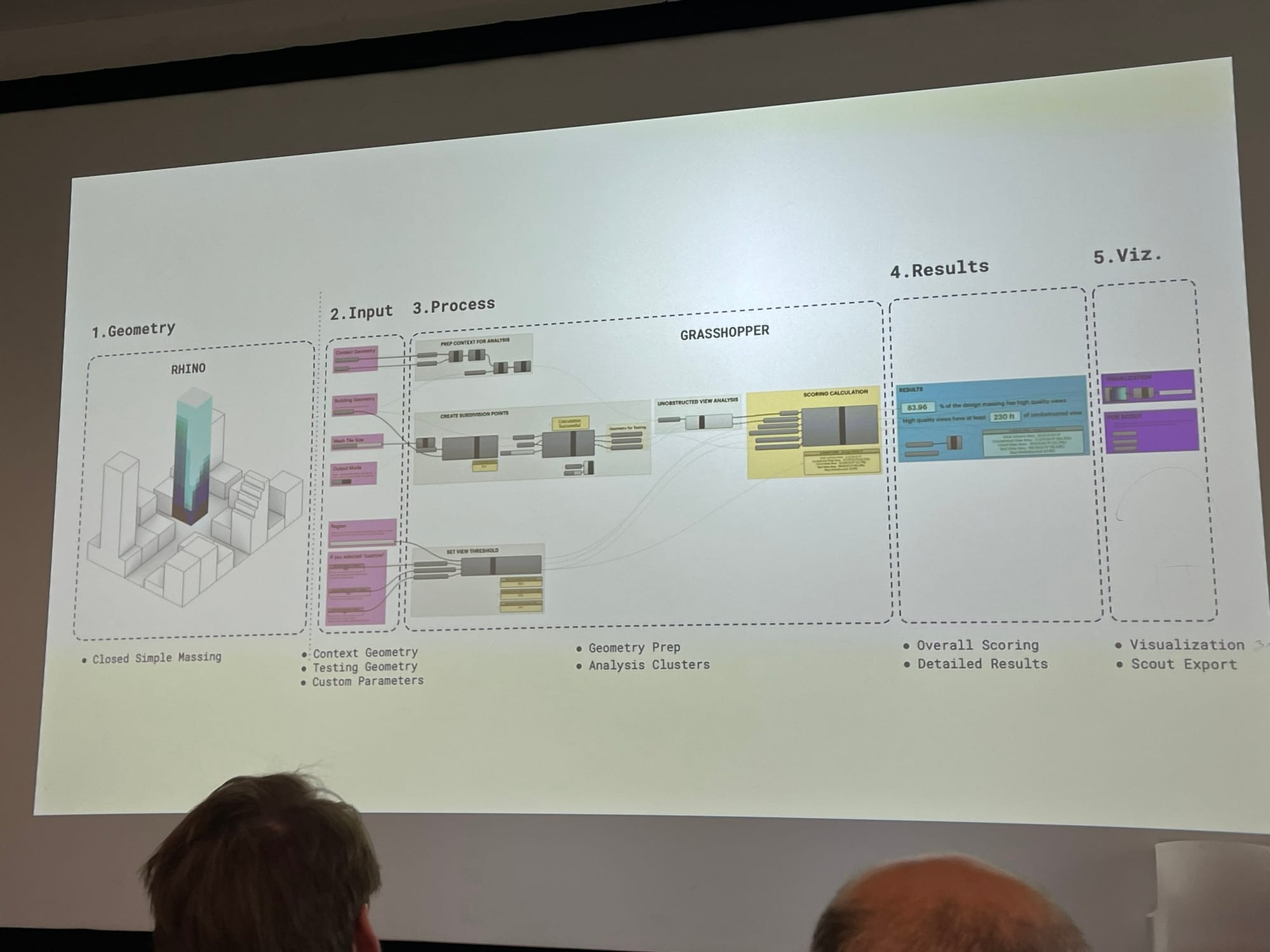
Branching Innovation: Timber Design and Construction with Computational Processes
Mark Skepasts, Structurecraft
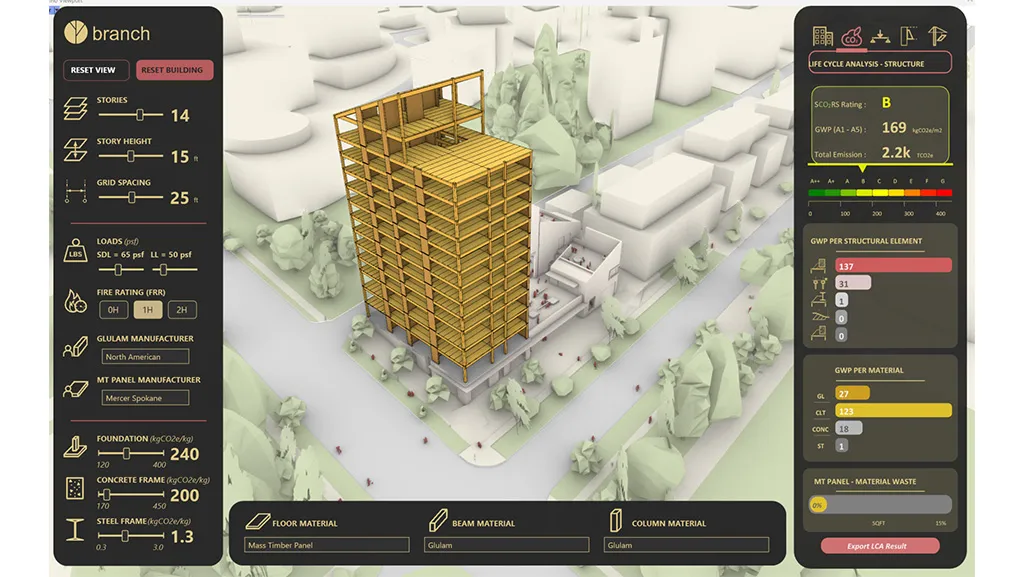
Structurecraft is a Canadian engineer-build (as opposed to design-build) firm that specializes in mass timber structures, which has built out a framework of web-app and Rhino plugin that greatly simplifies their development process for structural schemes and custom connections for timber joints. The framework, which is called Branch, offers engineers everything from conceptual ideation of different structural systems to detailed assembly design and automated shop drawing generation. They have made the conceptual ideation part of Branch available to the public, and it can be used to easily made quick comparisons between different structure types for a concept (link below).
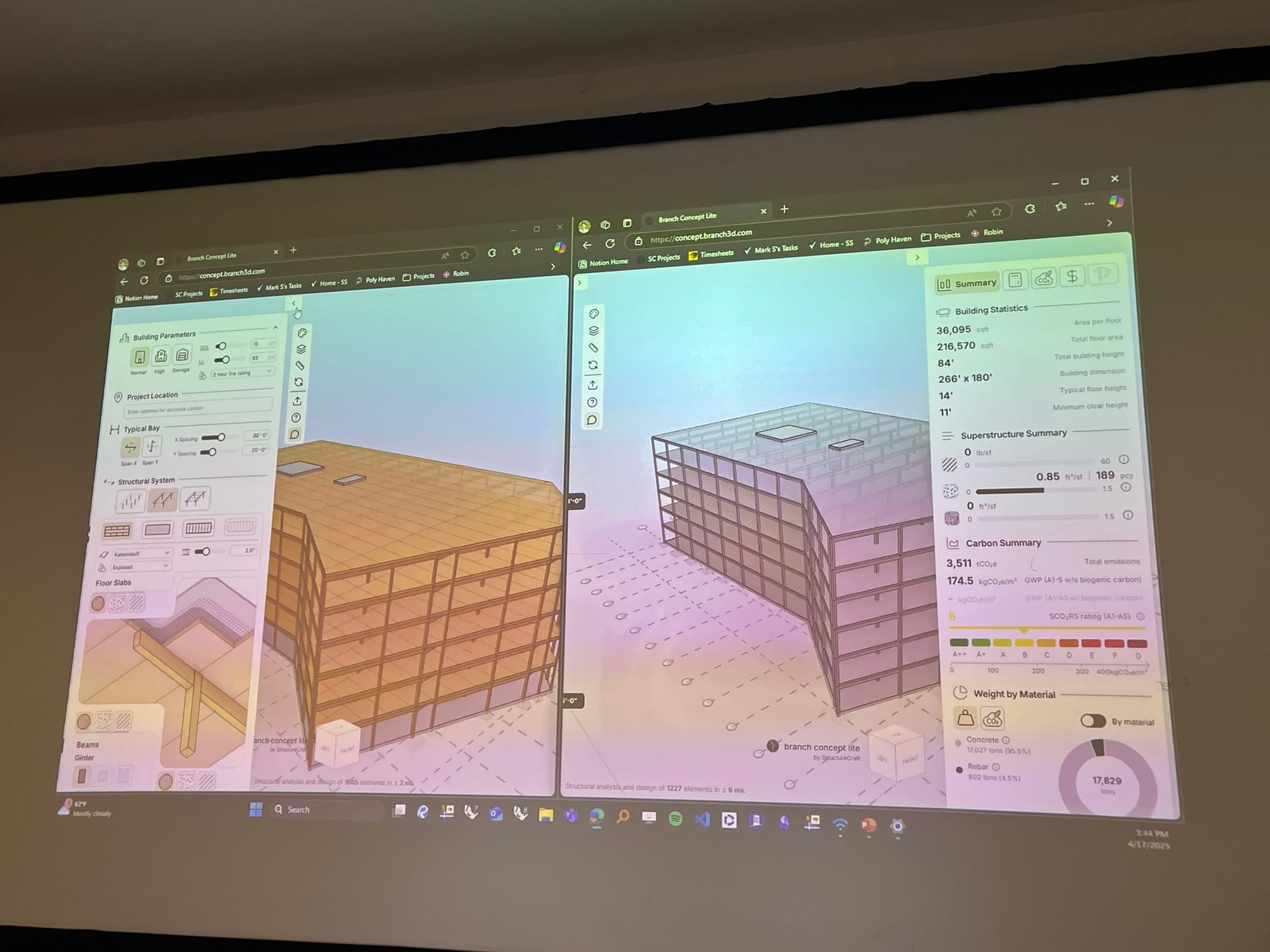
Real-time Performance-Driven Design and Optimization with Foster + Partners’ Cyclops
Oscar Borgstrom, Foster + Partners
Wocjciech Karnowka, Foster + Partners
Sherif Tarabishy, Foster + Partners
While this presentation was primarily focused on the recent release of the Cyclops plugin for Grasshopper, which dramatically reduces computation time for many of the most common environmental analysis simulations that architects use on a daily basis, the presenters did talk a little about software development efforts at Foster. The Applied Research and Development (ARD) team is comprised of 29 computational designers and software developers (about 1% of the entire company). They have six areas of focus, each of which can be further subdivided into distinct software products used in-house (see photos below). Their decision to make Cyclops publicly available was based on the idea that the benefit to both the industry at large as well as the planet outweighed any possible competitive advantage. From what I saw, I don't think Foster + Partners is lacking in competitive advantage when it comes to proprietary software development.
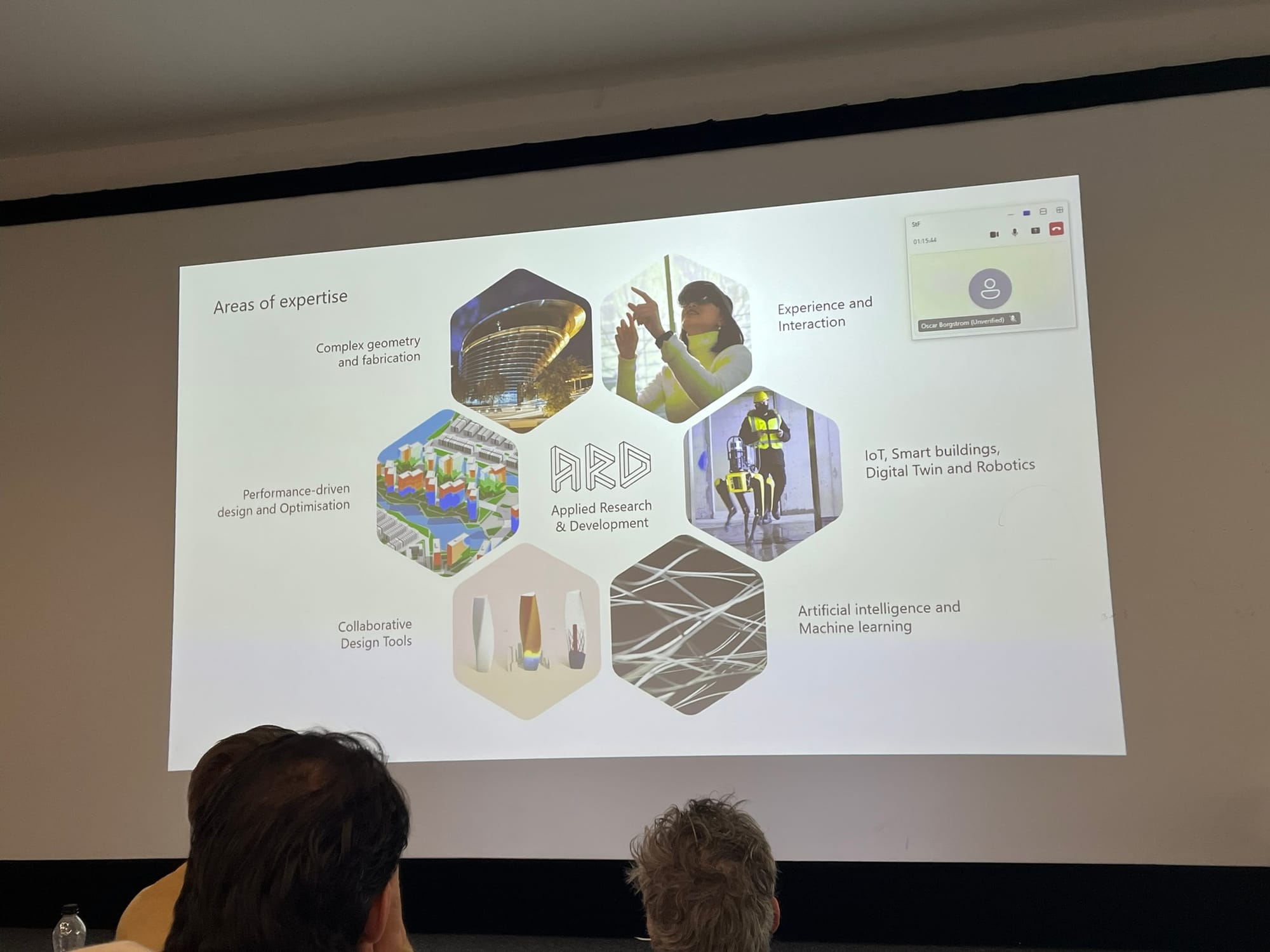

Theme 5: Last but not least, novel uses of Rhino and Grasshopper remind us that the potential for these platforms is limited only by their accessibility to people who have strong passions and innovative instincts.
One of the things I love most about the nerdy little world of Rhino-adjacent computational design is the punk-rock ethos of some of these projects. It seems like all you have to do to get something cool and new is take someone with a strong passion or interest in literally anything design-related and isolate them with a copy of Rhino for a year or two. These two presentations were definitely fan-favorites at Shape to Fabrication, as they reinforce the optimism that comes with potential and perhaps reinforce for all of us that we're interested in the right things and moving in the right direction.
Skatepark design – Form follows movement
Ebbe Lykke, Glifberg-Lykke
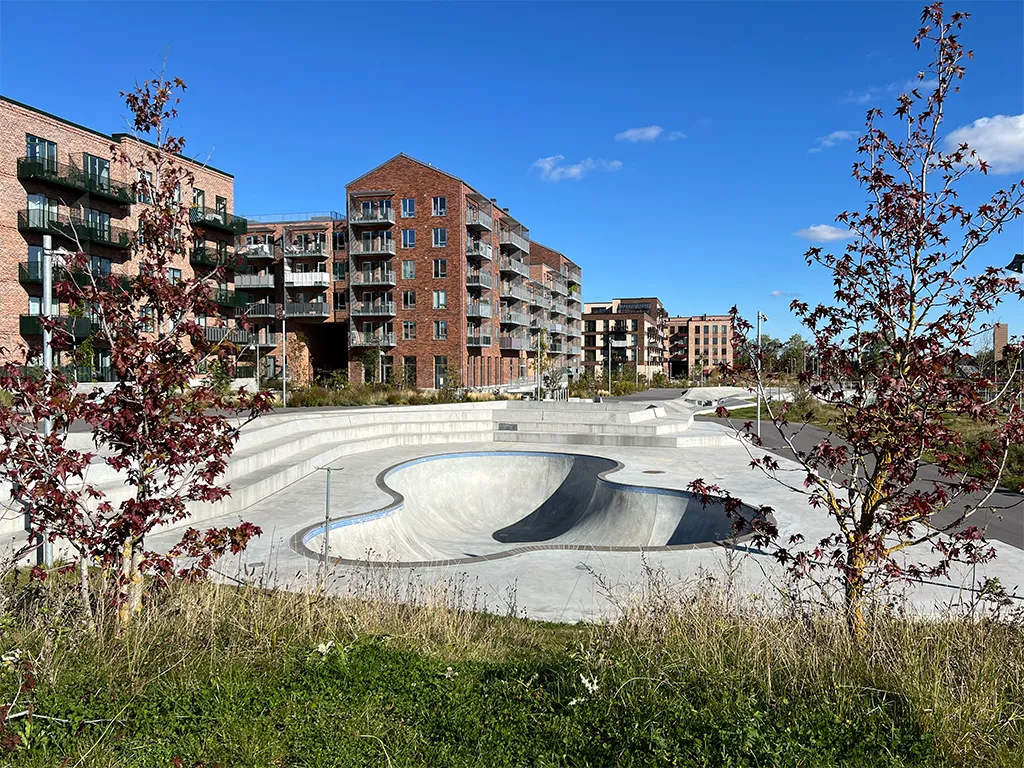
Ebbe Lykke, of Danish skate park design firm Glifberg-Lykke, outlined his firm's design process for generative the fluid, kinesthetic forms found in skateparks. The geometry of a skate bowl is, as you might guess, highly specific and directly impacts a skater's ability to get air or land a jump. Not only is the geometry important, but the cement surface must be carefully coordinated as well. As Lykke explained, all the craftsmen who build these parks are themselves also skaters who understand how the troweling process affects the movement of the skateboard trucks across the surface (yes, everything is 3x hand-troweled finish on top of a shotcrete base).
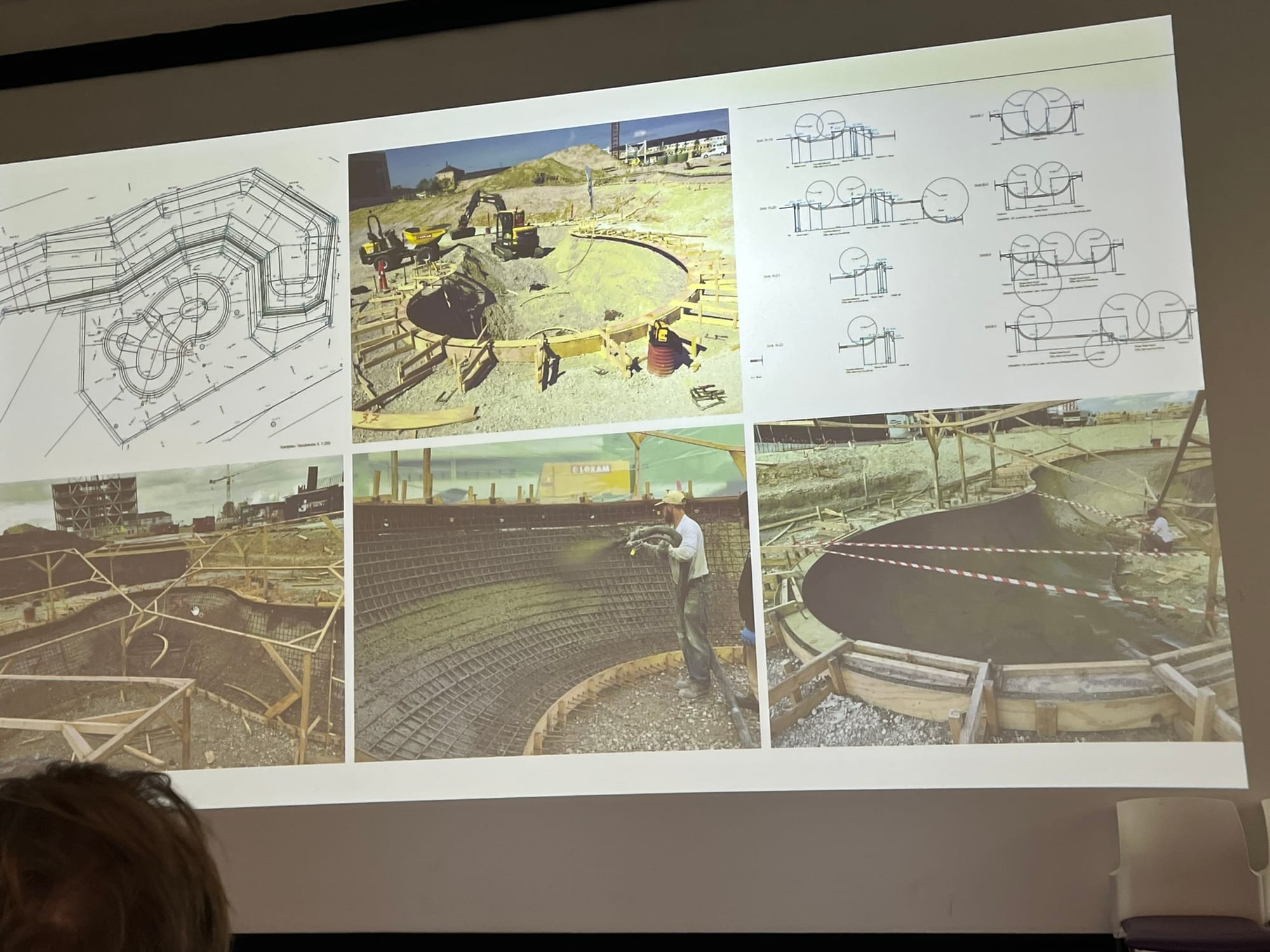
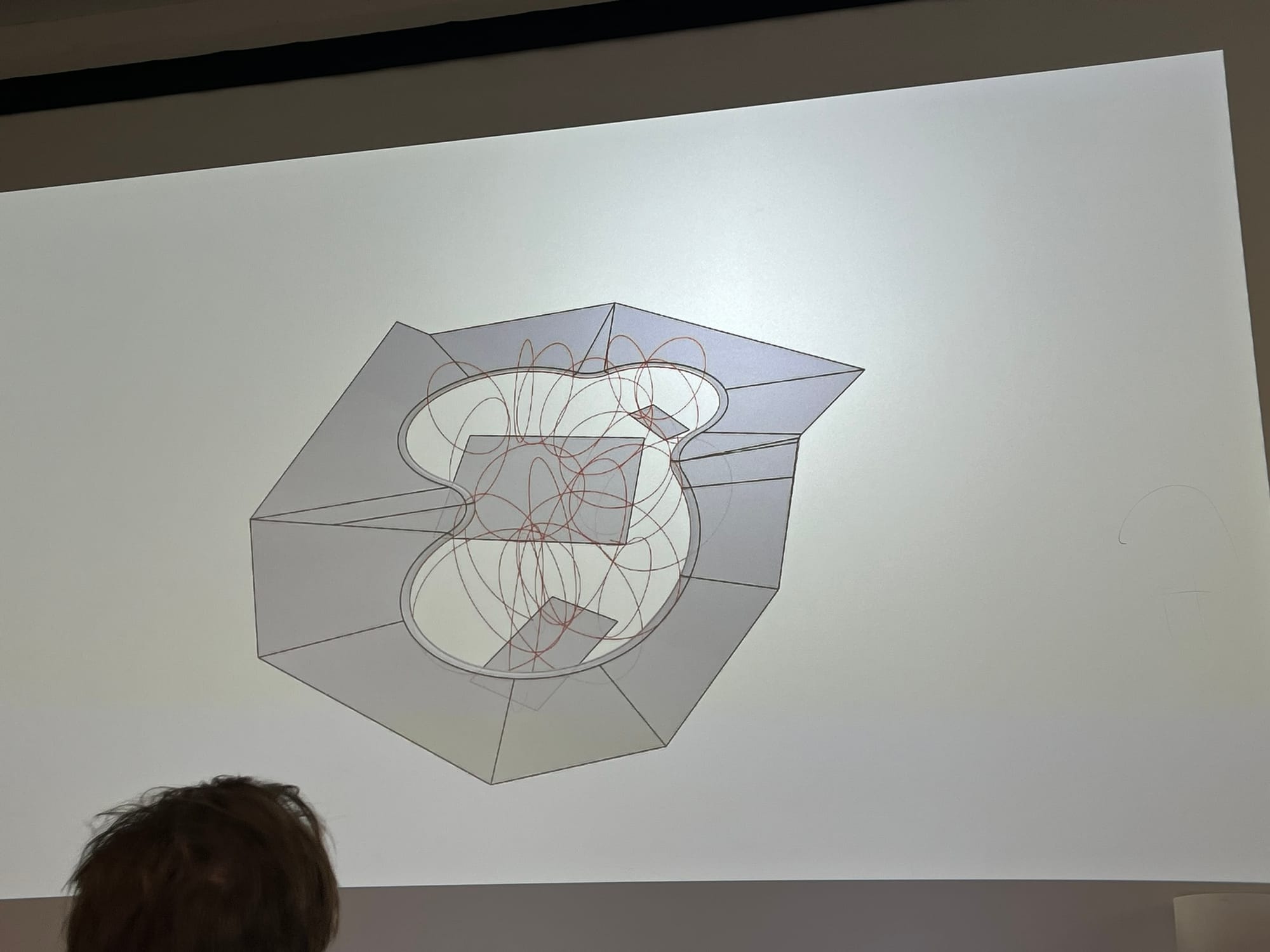
The Fit Formula: Crafting Bespoke Marathon Kit with Dimensional Garment Patterning
Elizabeth Bigger, Gencloth
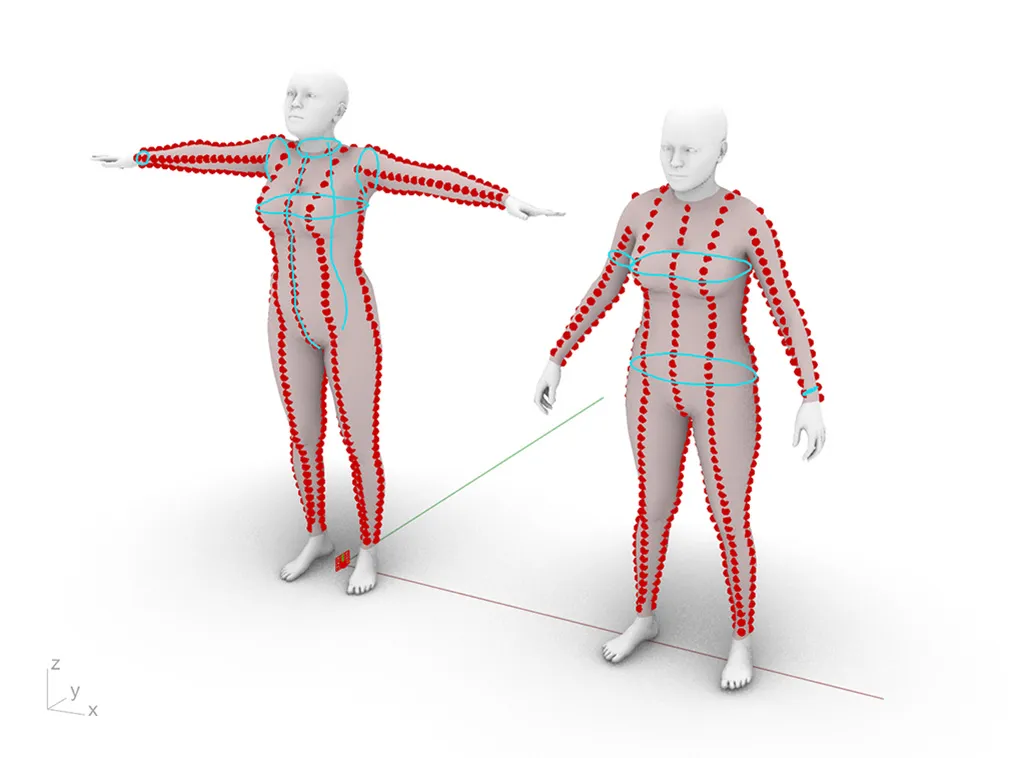
This was one of the last presentations of the conference and definitely one of the most interesting. Elizabeth Bigger, an American expat living in Spain, works as a computational garment practitioner and develops fascinating uses for computational design with regard to clothing and how we dress ourselves. Her GenCloth project is an attempt to push back against the notions of mass-produced clothing that can be worn by anyone and fits no one. Through body scanning and computationally-defined clothing patterns, she has been able to create one-off patterns for truly custom clothing, in an attempt to rejuvenate the nearly-forgotten art of pattern drawing for garments.
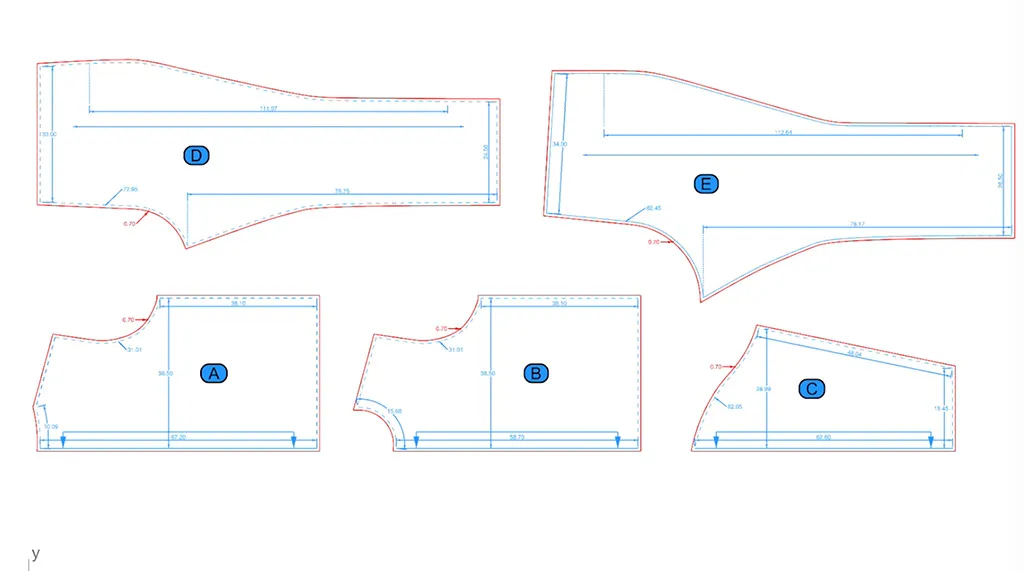
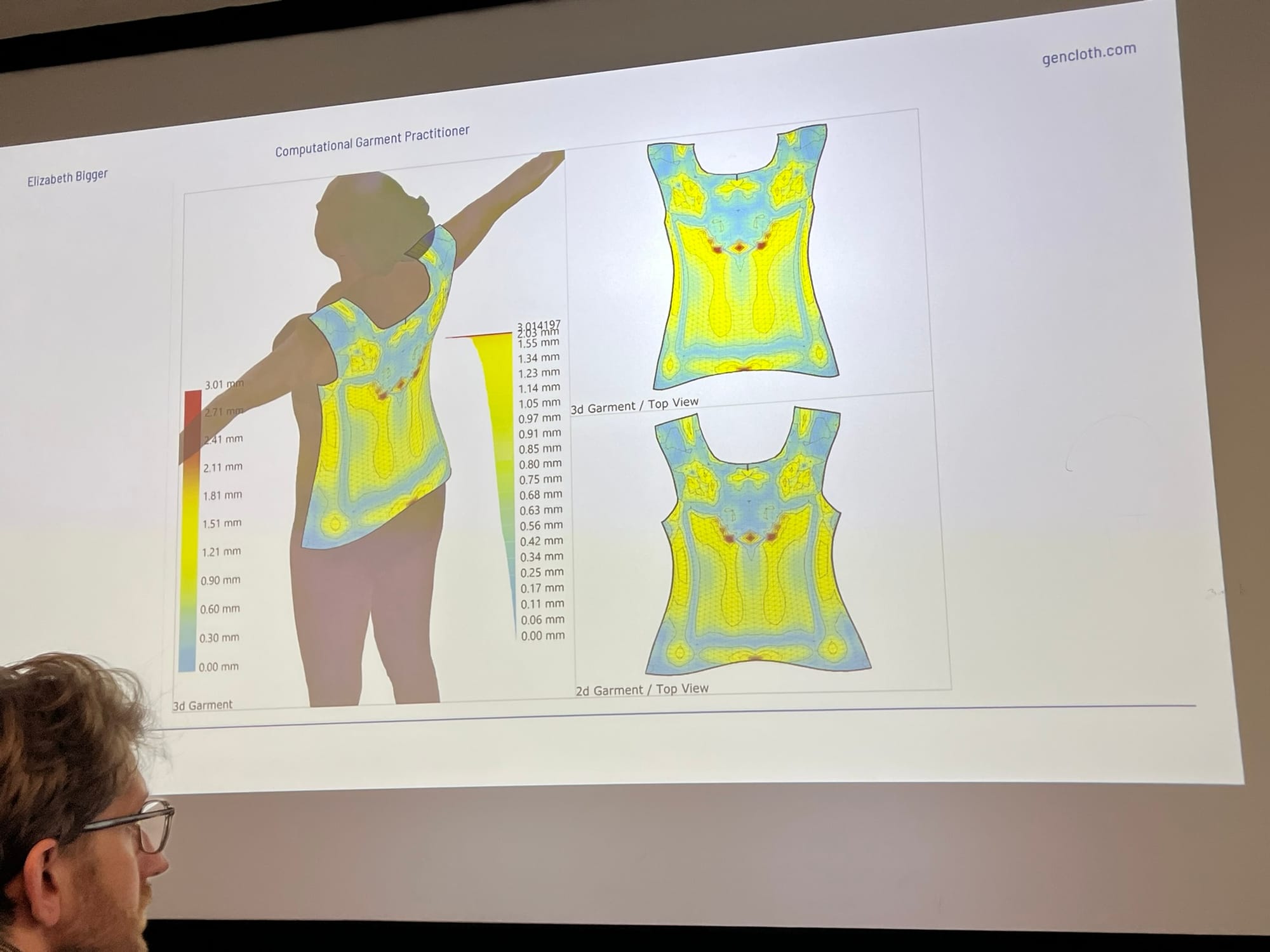
To wrap it all together
If you've read this far in my recap of Shape to Fabrication '25, kudos to you and thank you for trusting my reporting enough to spend however long it took you to get here. This was my first time at Shape to Fab, and I heard from many that this year's offerings were more idiosyncratic, more practice-focused, and more genuine than in previous years. I couldn't really say, but I did find the overall collection of expertise and passion to be really quite special. If you have the opportunity to go to London in 2027, I definitely recommend it. Unfortuantely, there's a lot that didn't make it into this report. I have plenty more to share, but I have to cut it off at some point or else this page will never be published. Don't hesitate to drop a comment below or get in touch directly if you want to hear more about anything I saw.
Comments ()